Team: Musab Badahdah, Namthaja Additive Manufacturing Solutions
Client: Dammam Amana, 2021
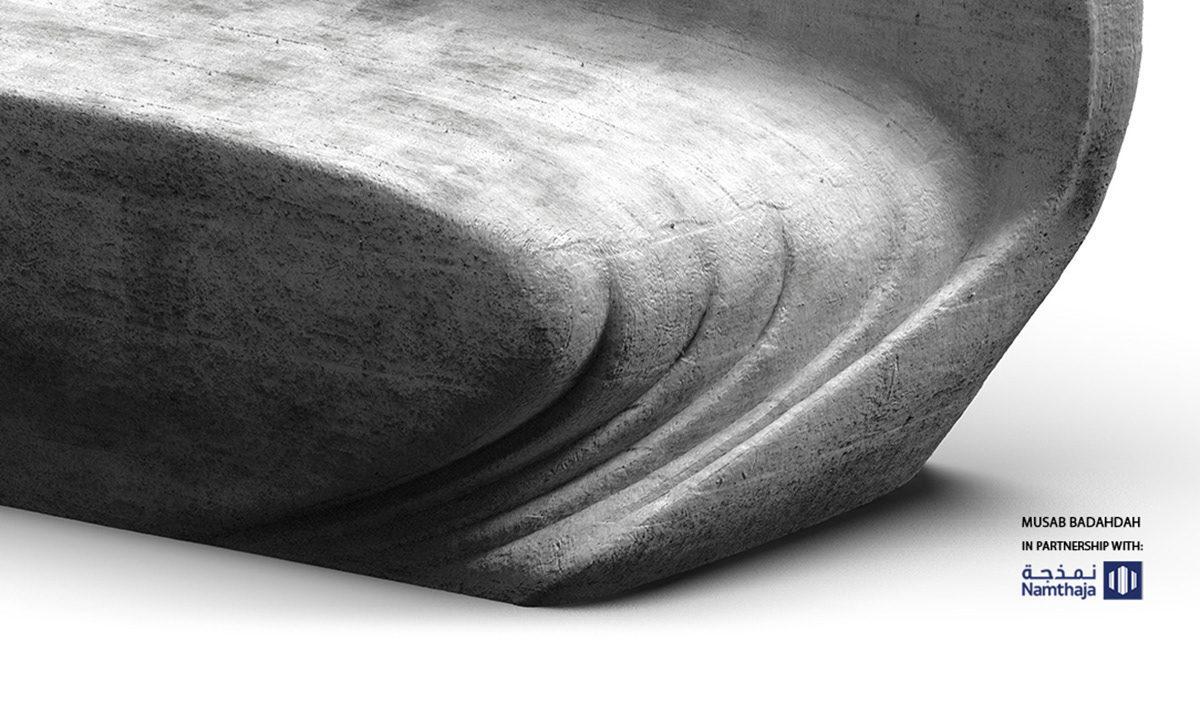
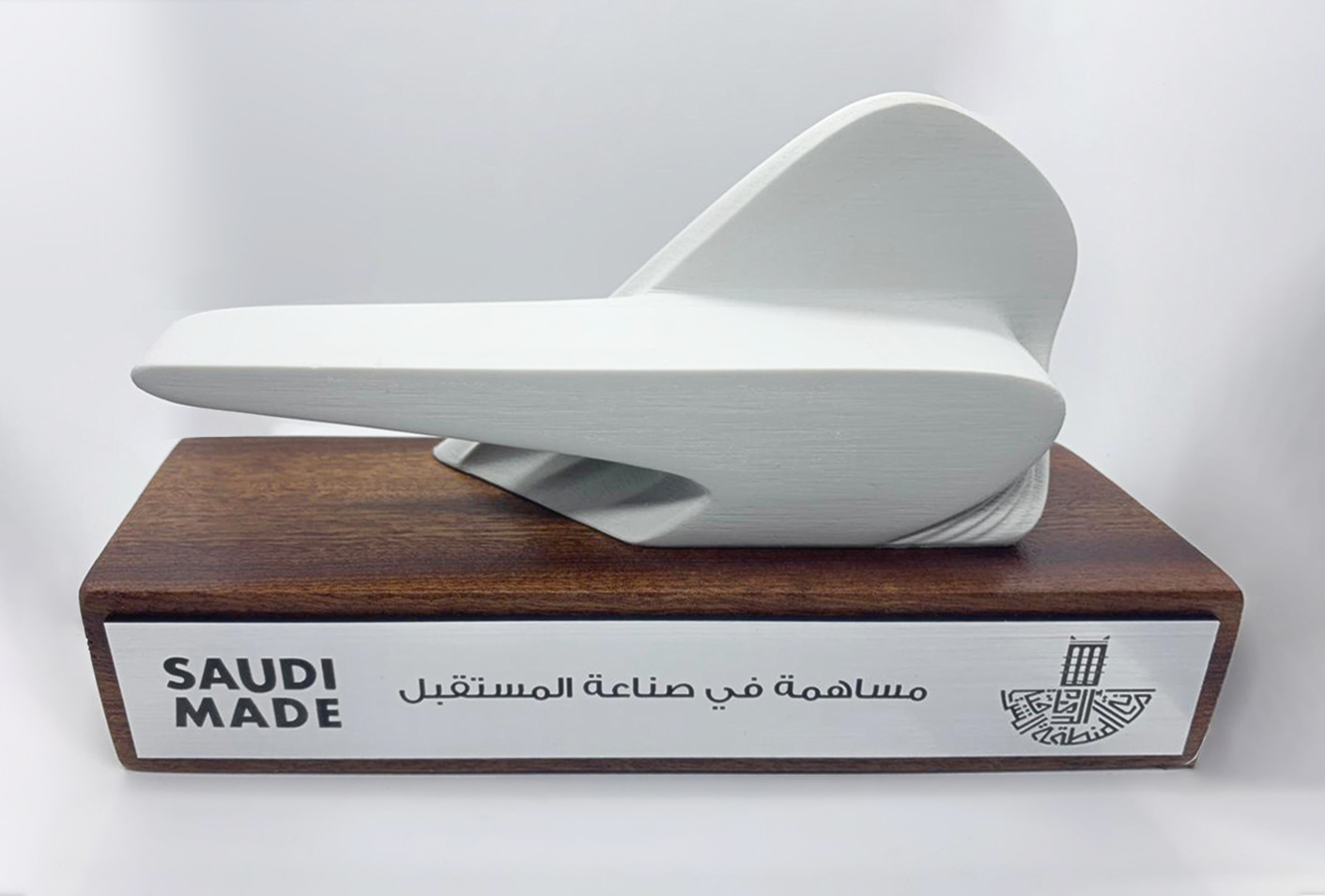
3D printing is one example of the additive manufacturing technology. It is a technological advancement made possible by the transition from analog to digital processes. It bridges the gap between design and literal production. It skips the human error, overlapping tasks and reduces the time required.
It is not limited to small pieces or artifacts. It goes to bigger scale such as this piece furniture or even larger architectural and construction elements. Many applications are surfacing that shows how precise and delicate this technology is to create actual replica of the digital design. The design can be printed over and over like printing any sheet of paper
3D printing does not only mean to have a final product fresh out the printer. The products could be polished, treated, painted and coated to have a better finishing surface. More importantly, It could be a major step on the production process where the 3D print is actually a mold or a template that could be used for mass production. And this what we see here.
The formwork has been printed using plastic. Then treated with fiberglass to have one solid formwork for mass production. Eventually the treated formwork of the 3D print is used to cast the concrete that you are seeing right here. One 3D print, one forme work, hundreds of concrete benches as you’d like
Introduction:
Digital design and 3D printed concrete bench prototype for 1:1 scale
3D printing is one example of the additive manufacturing technology. It is a technological advancement made possible, by the transition from analog to digital processes in fabrication. It bridges the gap between design and literal production. It skips the human error, overlapping tasks and reduces the time required.
It is not limited to small pieces or artifacts. It goes to bigger scale such as this piece furniture or even larger architectural and construction elements. Many applications are surfacing that shows how precise and delicate this technology is to create actual replica of the digital design. The design can be printed over and over like printing any sheet of paper.
3D printing does not only mean to have a final product fresh out the printer. The products could be polished, treated, painted and coated to have a better finishing surface. More importantly, It could be a major step on the production process where the 3D print is actually a mold or a template that could be used for mass production. And this what we see here.
The formwork has been printed using plastic. Then treated with fiberglass to have one solid formwork for mass production. Eventually the treated formwork of the 3D print is used to cast the concrete that you are seeing right here. One 3D print, one form work, hundreds of concrete benches as you’d like
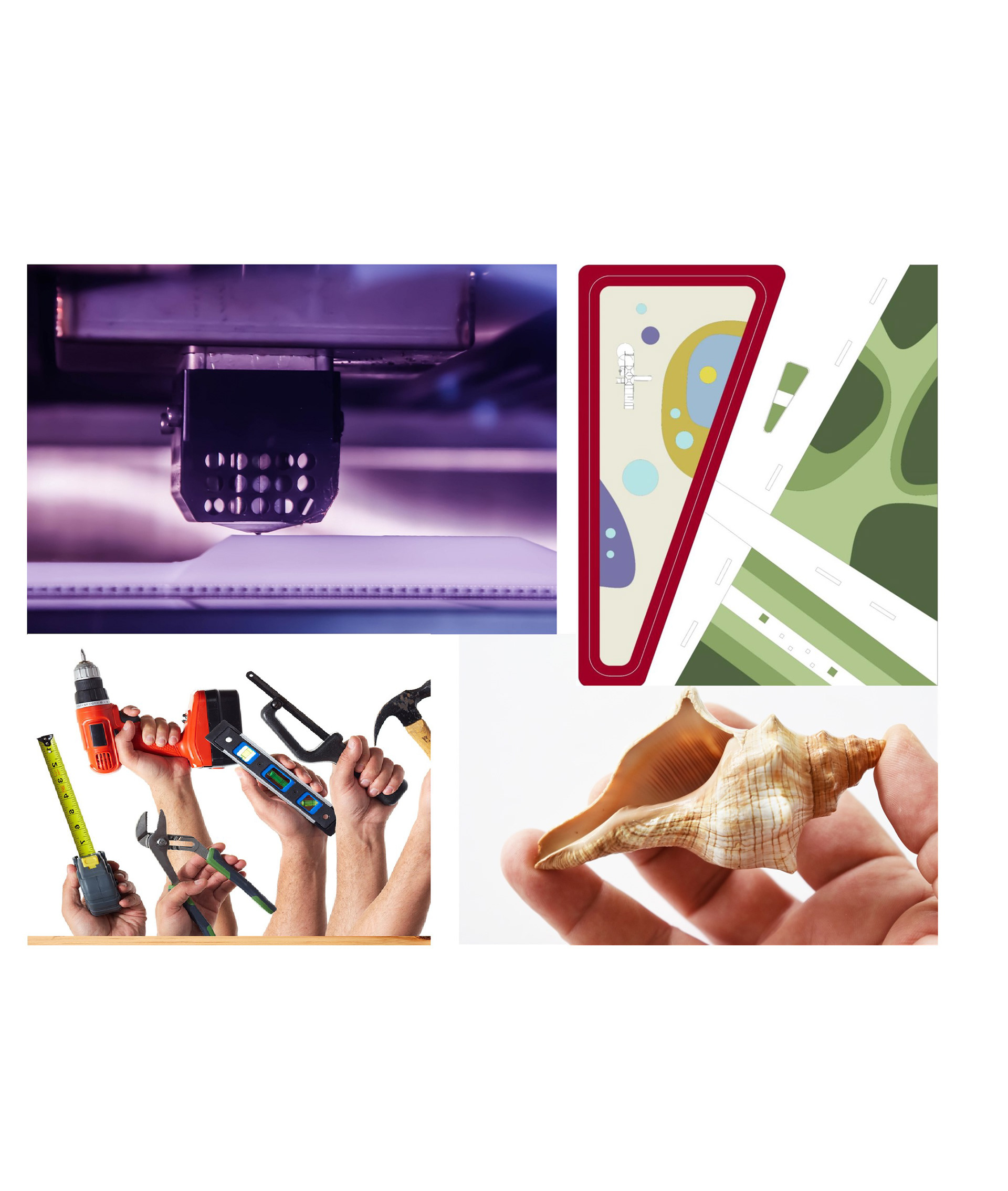
Finding common terminologies and by abstracting main profile of each item, a scenic sense of smooth curvature with floating edges and subtle details is more likely the way to go.
A rough diagrammatic composition was generated to predict a powerful blend of previous abstraction. The composition contain the main three elements blended in a way that are subtlety dominant and crisp details that are unique.
As challenging design it is, yet it’s properly functioning. Half is structurally stabled cantilevered and the other with back rest as counter balance. “It is not how usually see concrete”
The design was created to provide different details and aesthetic as you move around. Each angle has it own unique composition and perfect tectonic that are signature in concrete manufacturing.
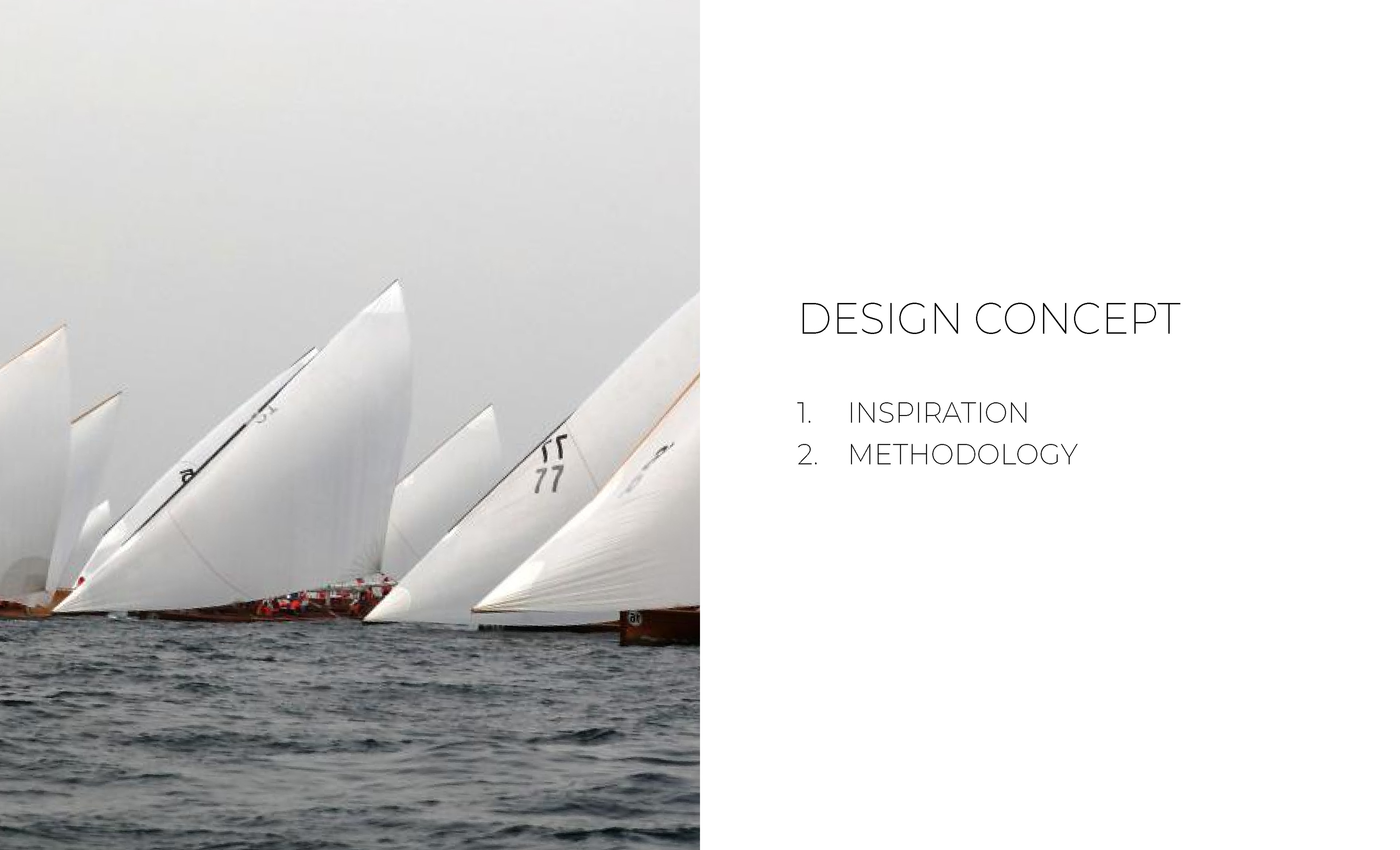
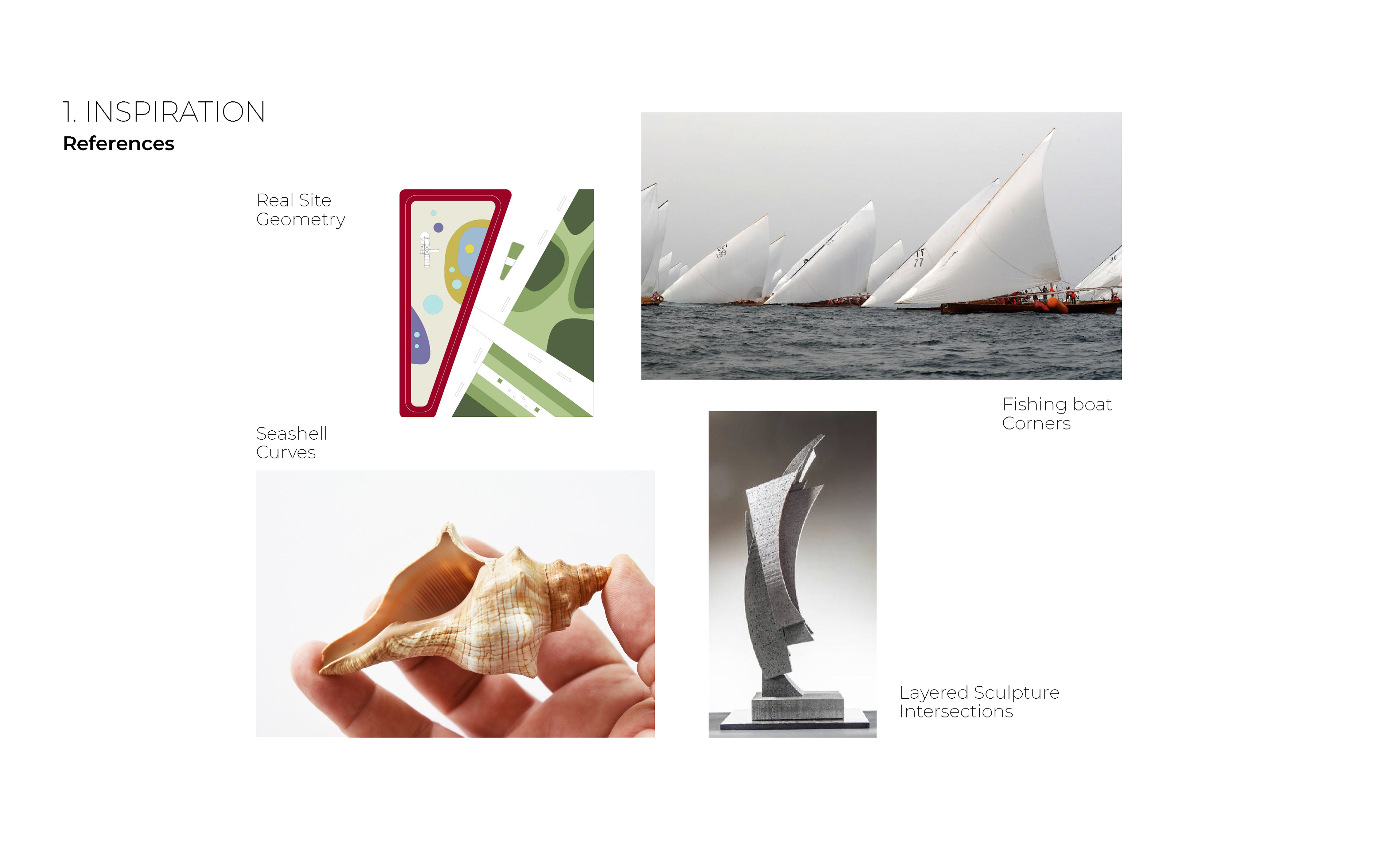
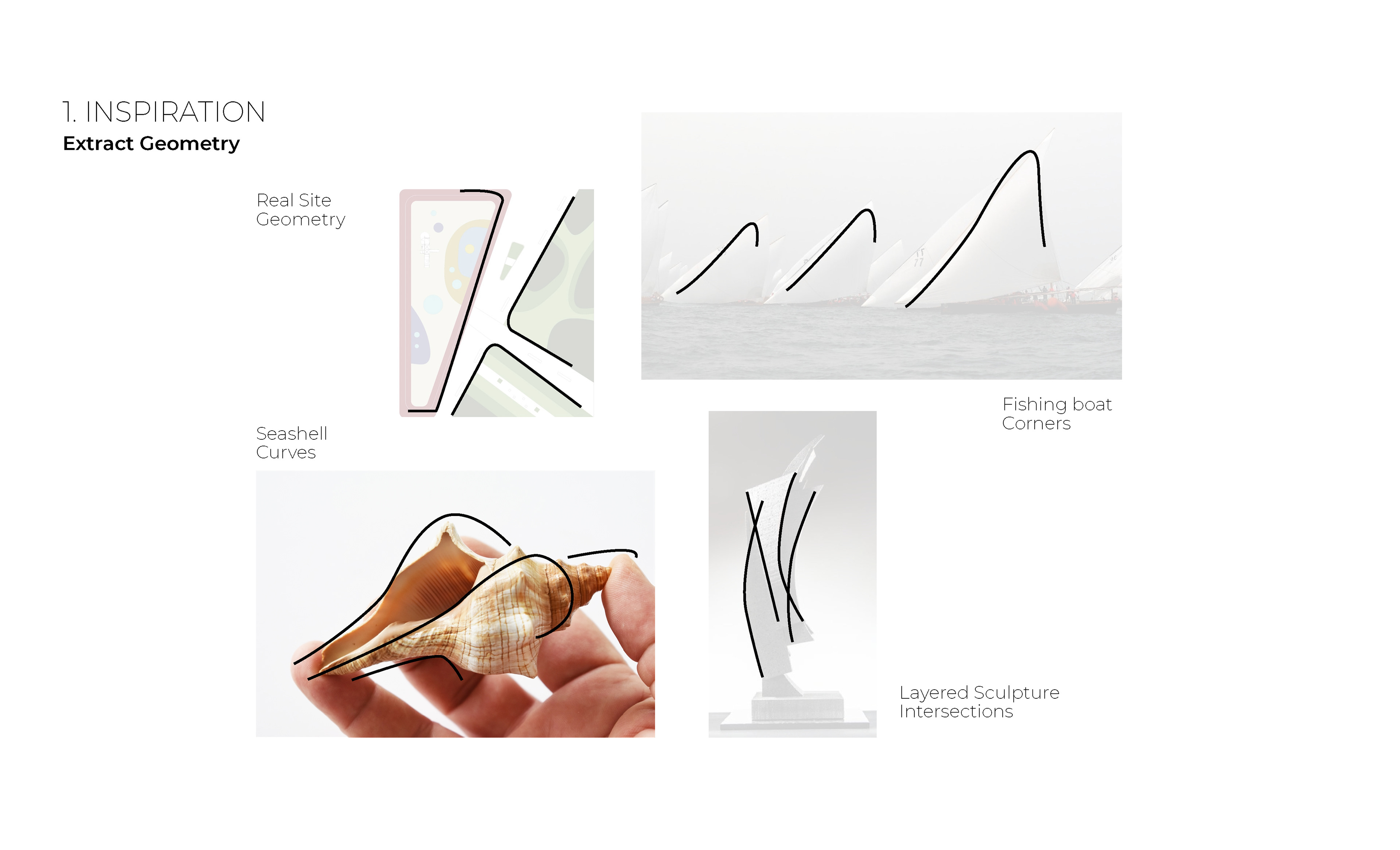
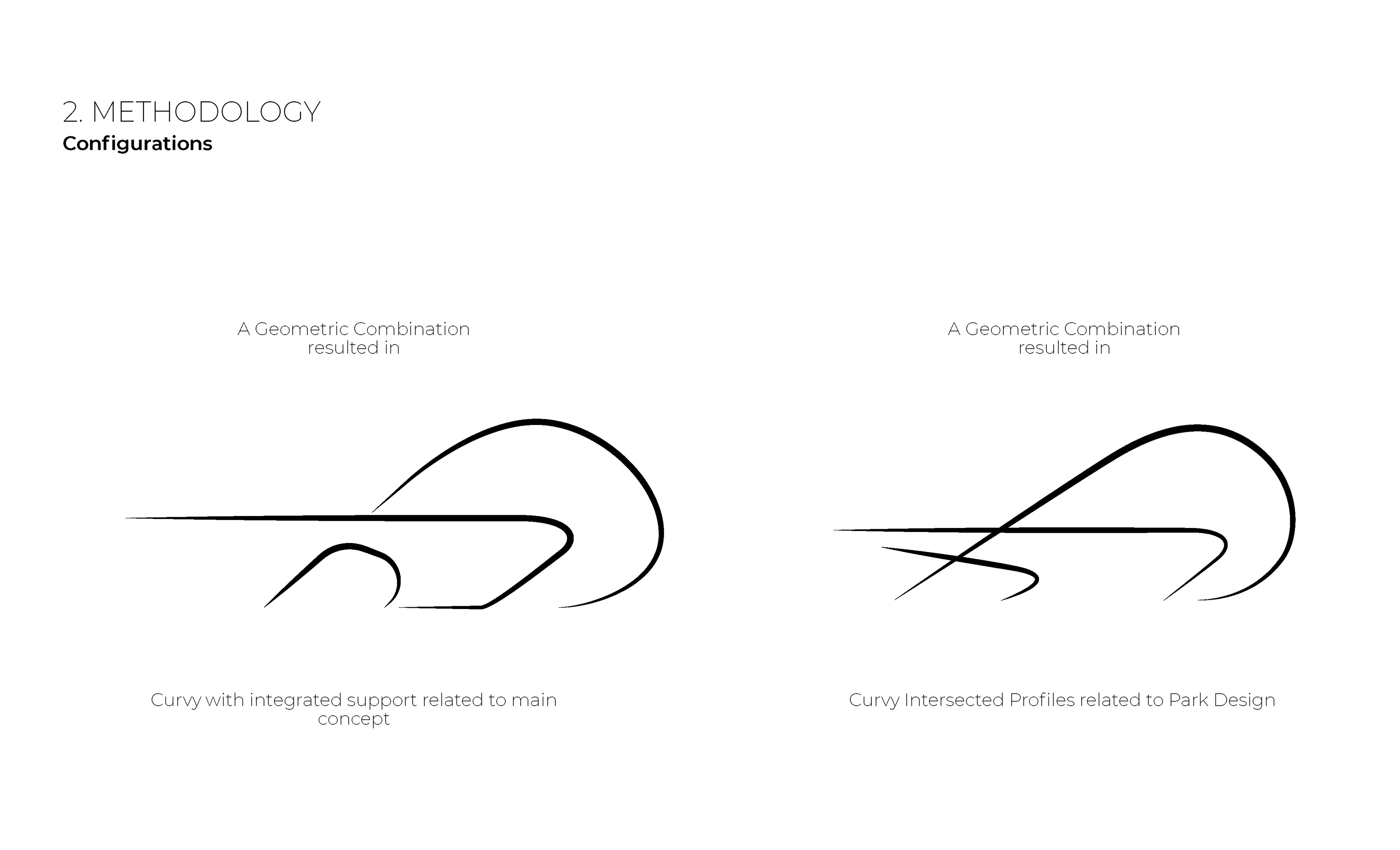
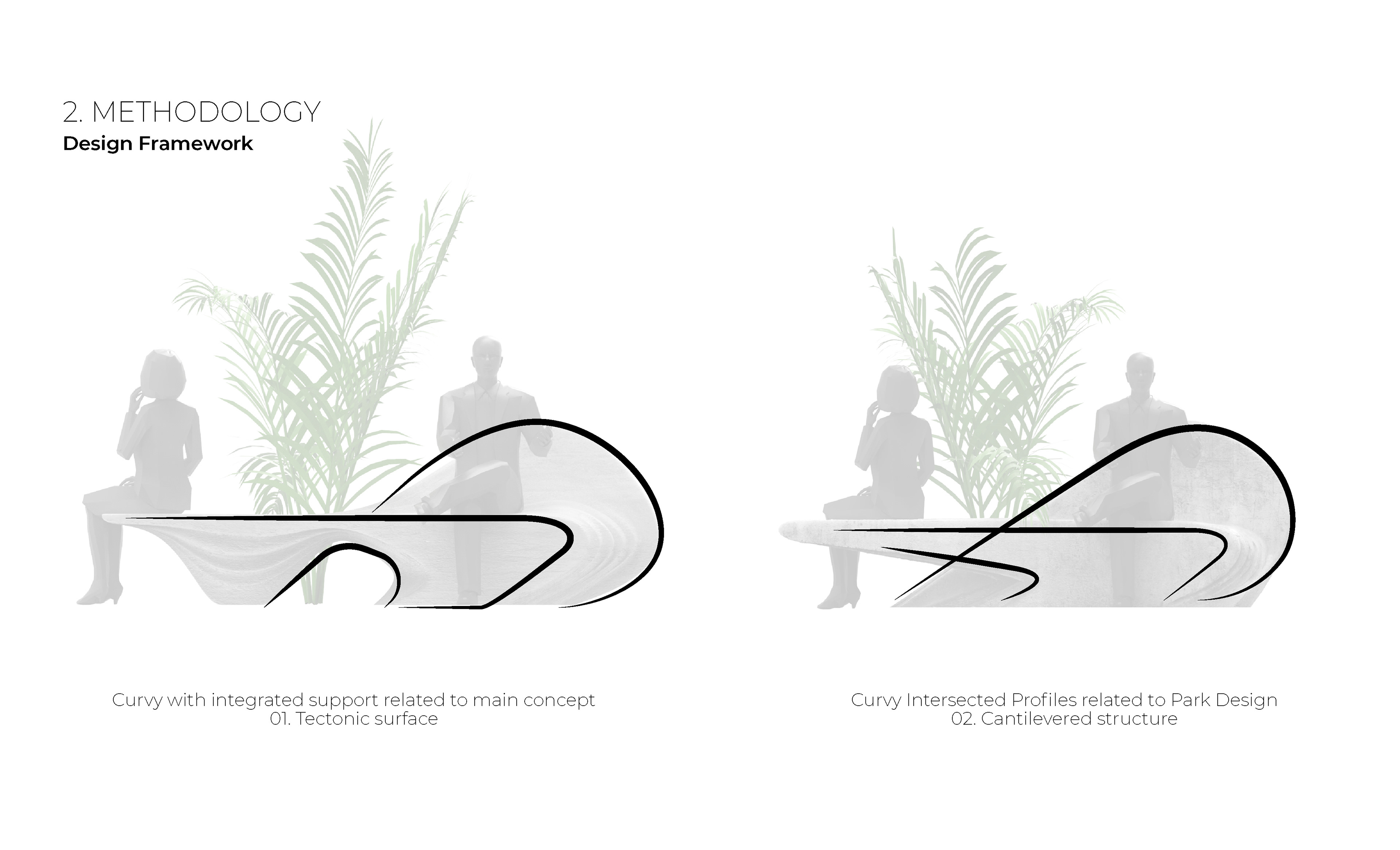
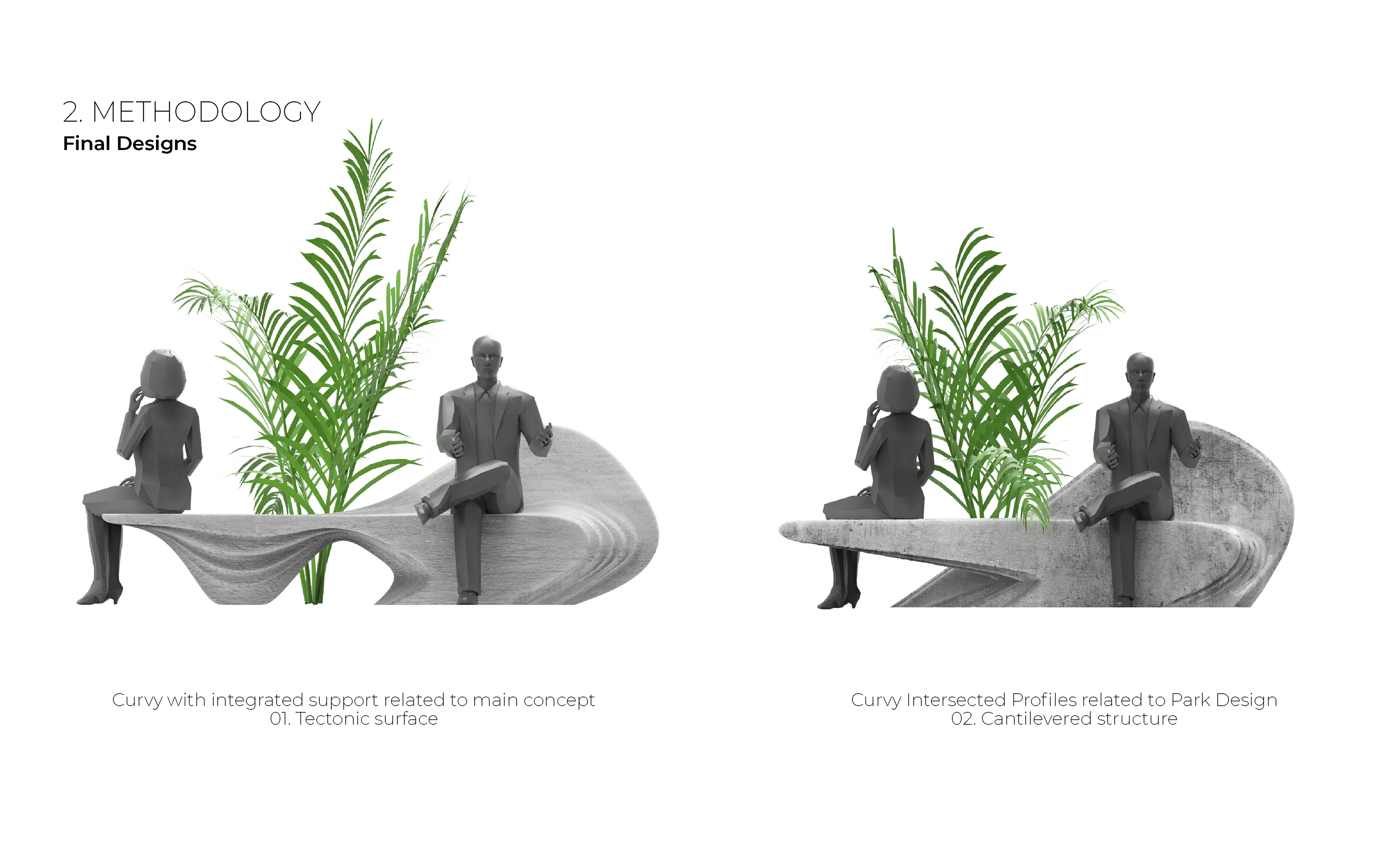
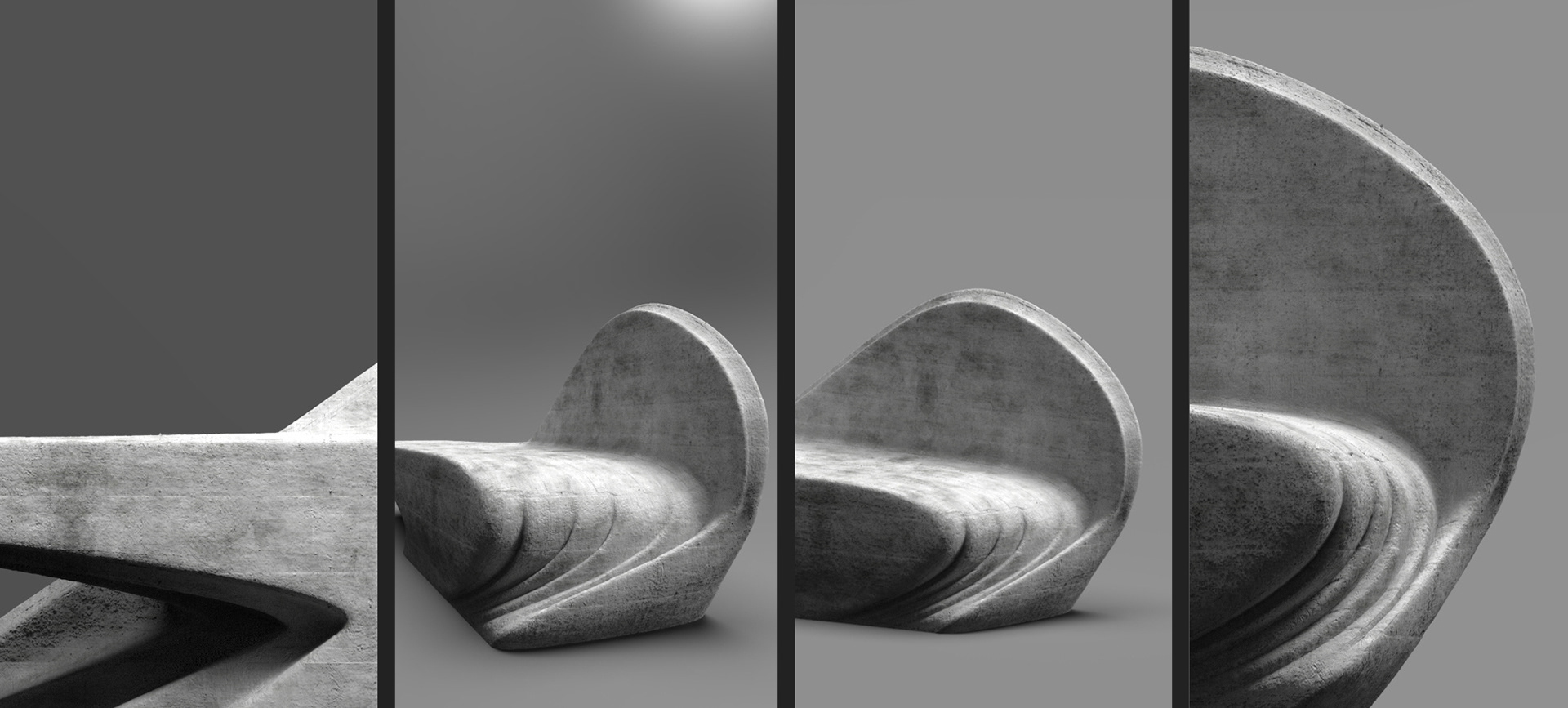
It is not how usually you see concrete. The goal was to emphasis the power of technology to make concrete do things it usually doesn’t do. With soft looking and smooth curvature, it doesn’t feel rigid but might fell like sponge. Concrete usually under compression, but it’s not visible as the only way to see it is as cracks. But this design intended to shoe the compression as if it soft object is under pressure.
– A proud moment when people poke the waves to check if it solid enough to set on.
– When people ask is this concrete?
– Or when they sit in the middle and slowly slide to the cantilever.
– And finally when they challenge the design to see if it break, but it doesn’t.
– A proud moment when people poke the waves to check if it solid enough to set on.
– When people ask is this concrete?
– Or when they sit in the middle and slowly slide to the cantilever.
– And finally when they challenge the design to see if it break, but it doesn’t.
After the design is completed and ready for fabrication. The model goes into many steps until it is ready for printing. It basically through an optimization process to make sure it satisfices the process and the technicality of the printing methods. And to avoid all unnecessary geometry that would cause errors or take more time in printing.
In this step, we print the parts individually then assemble them as on piece.
Testing, testing and testing the key success from design to fabrication.
It was impossible to build this bench in any other way except by 3D printing method. Many contractor couldn’t do it. Others estimated 2 to 3 weeks to build the formwork.
Our 3D capabilities allowed us to build the mold and pour concrete in less than a week.
Testing, testing and testing the key success from design to fabrication.
It was impossible to build this bench in any other way except by 3D printing method. Many contractor couldn’t do it. Others estimated 2 to 3 weeks to build the formwork.
Our 3D capabilities allowed us to build the mold and pour concrete in less than a week.
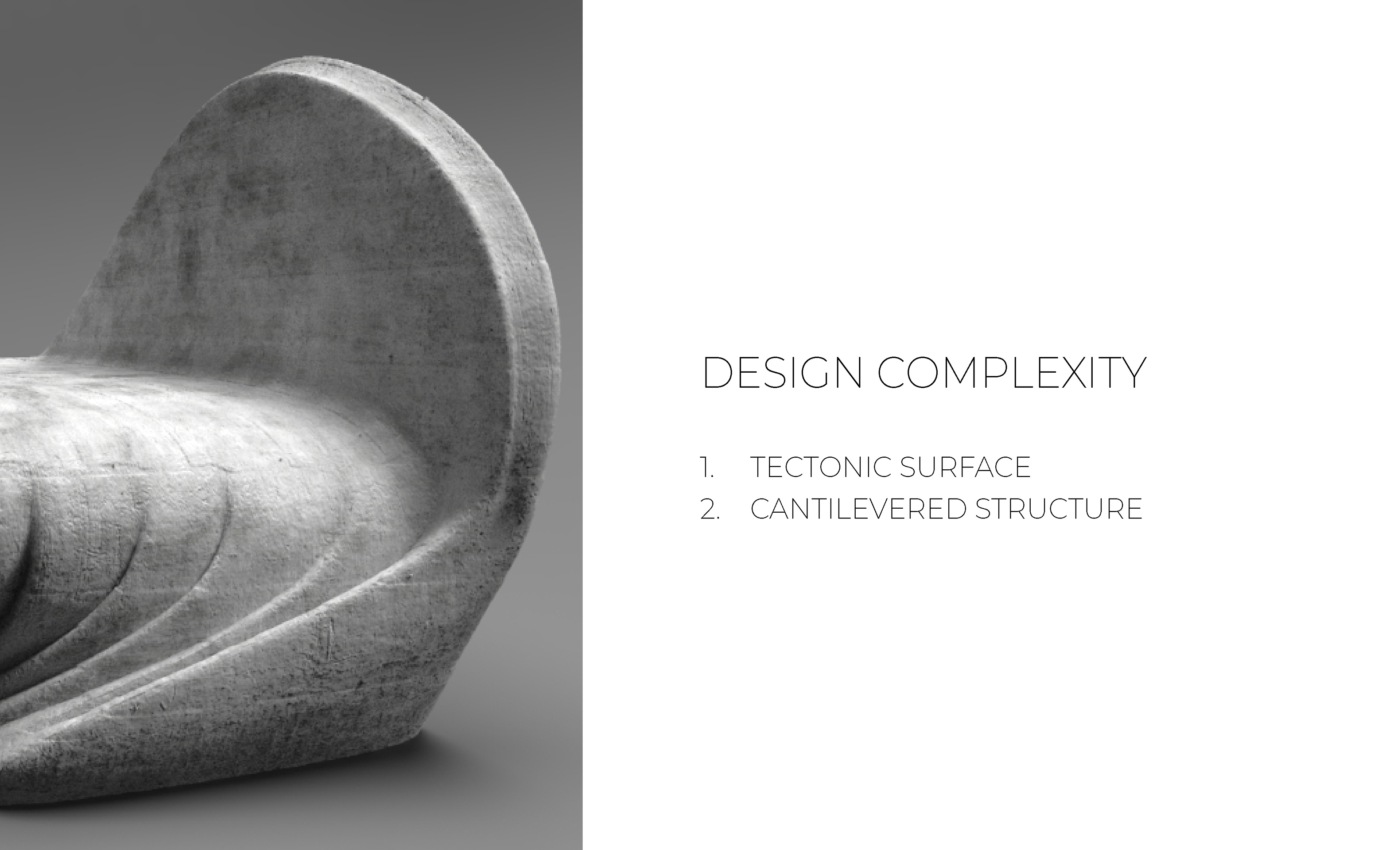
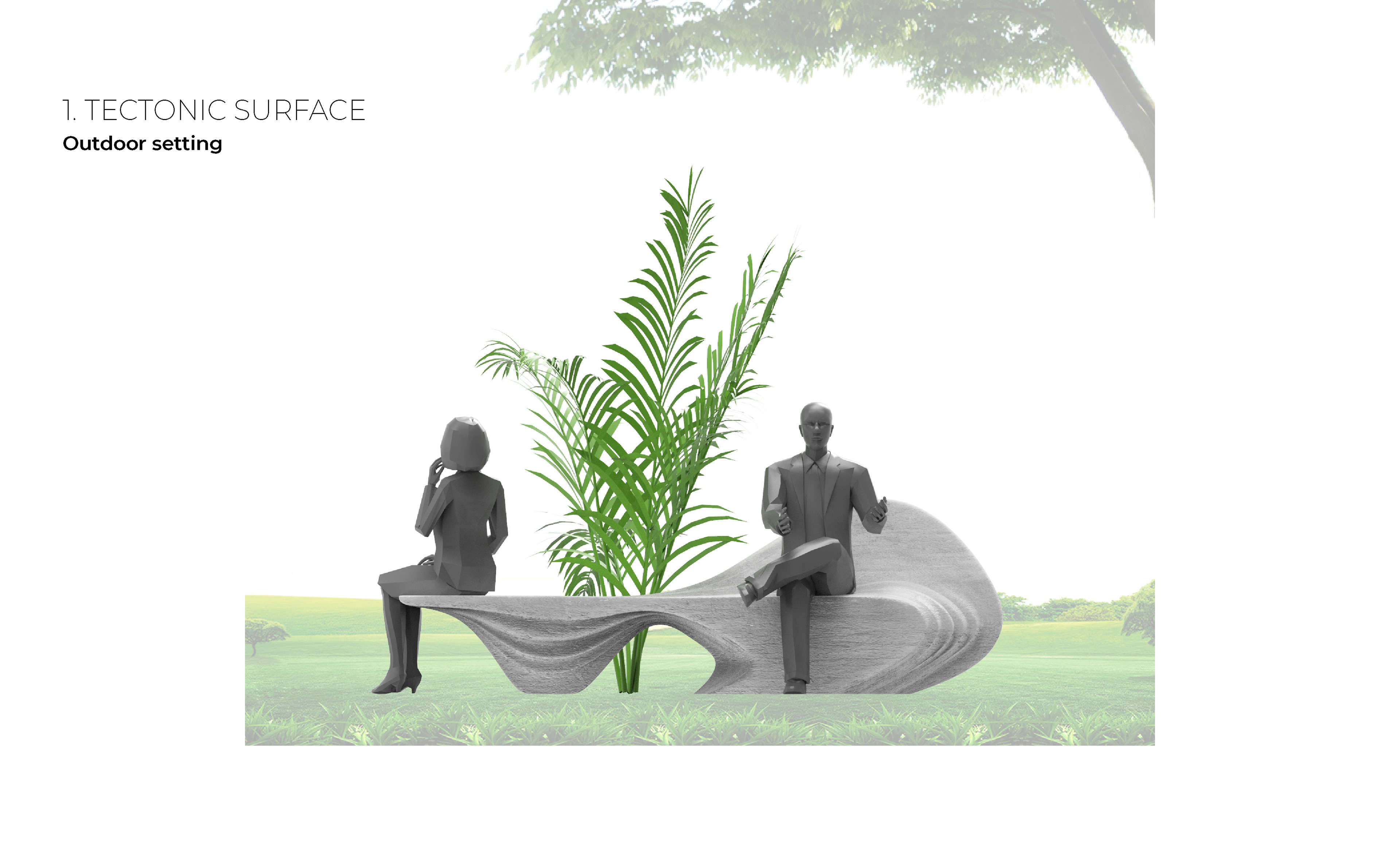
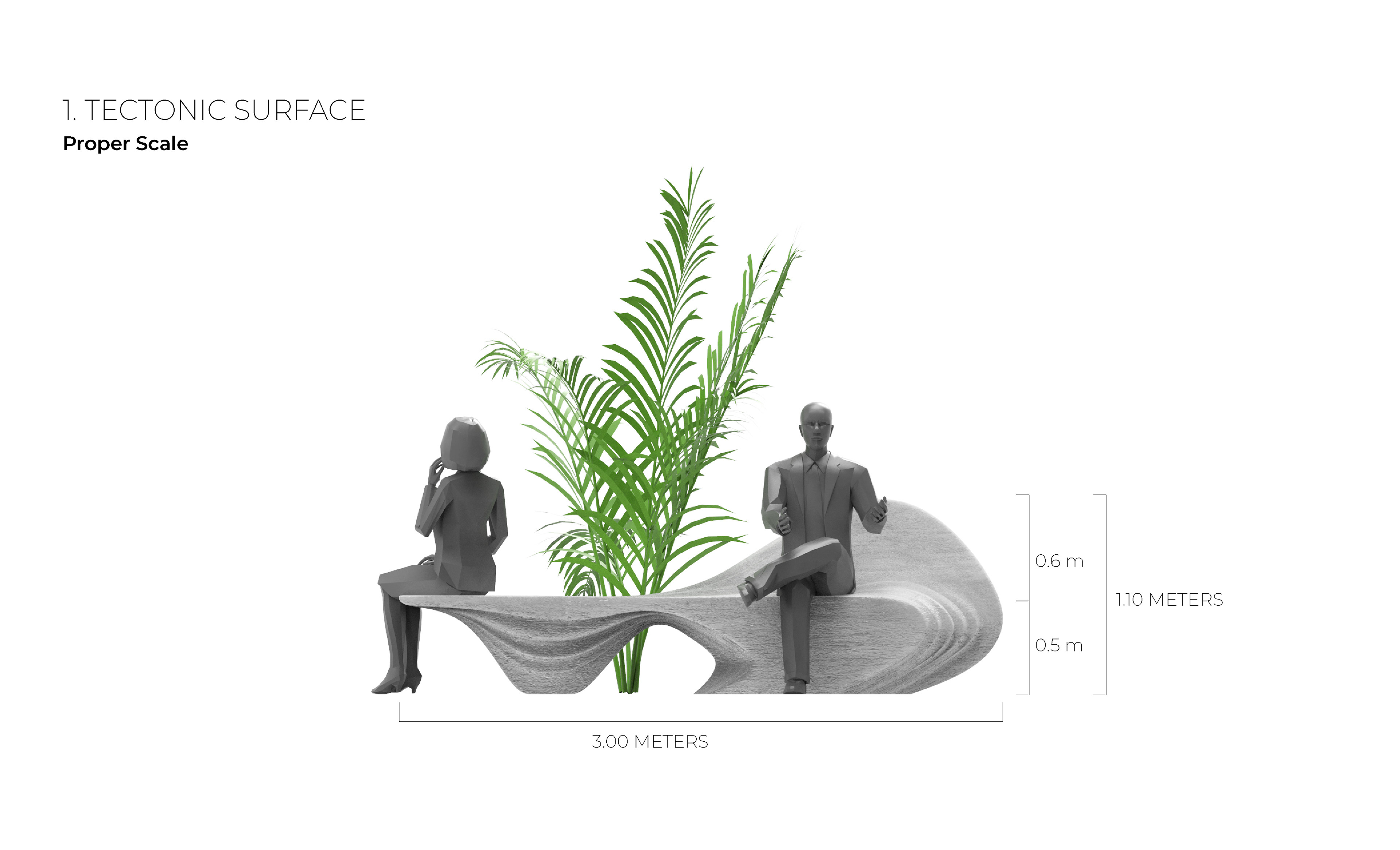
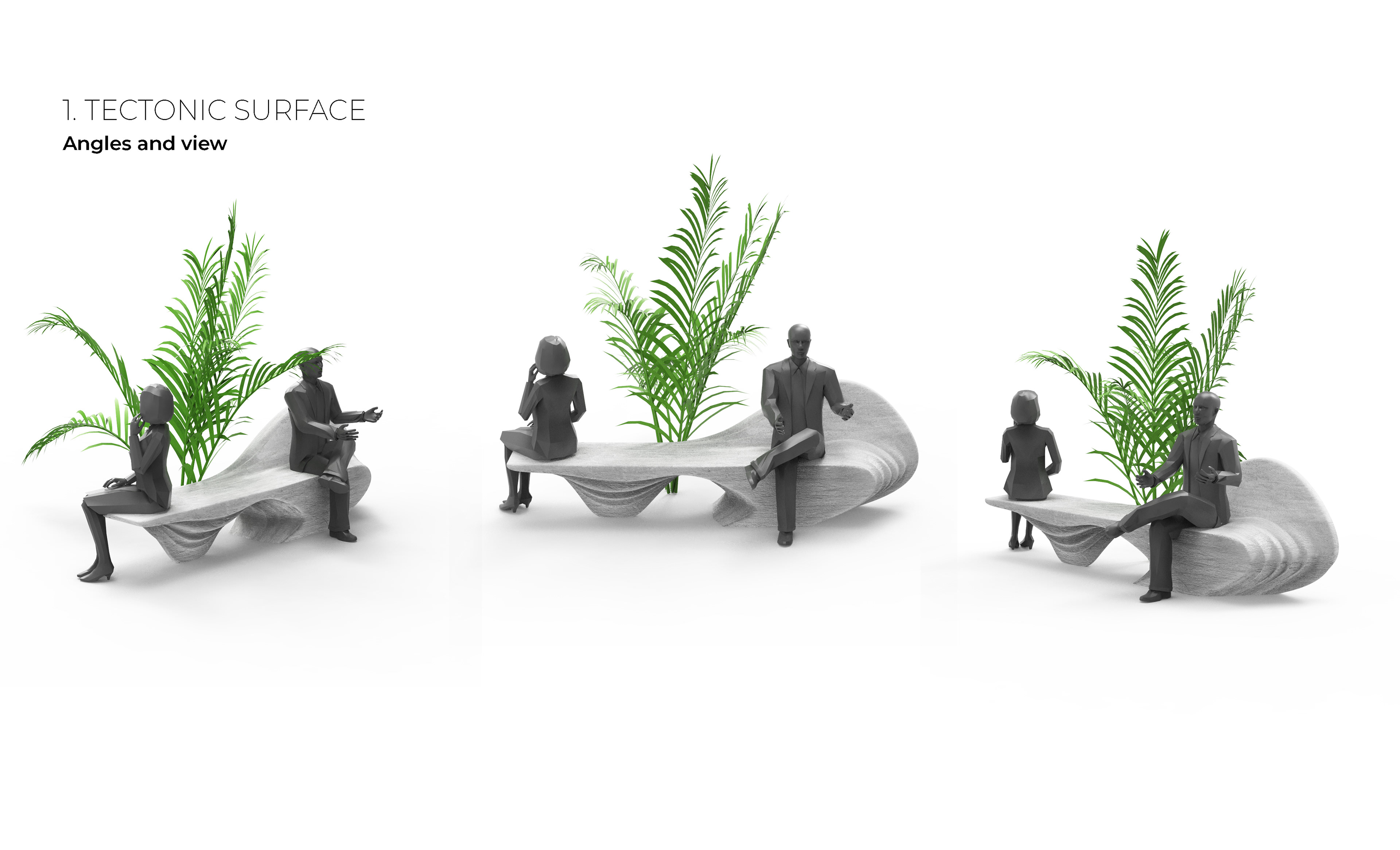
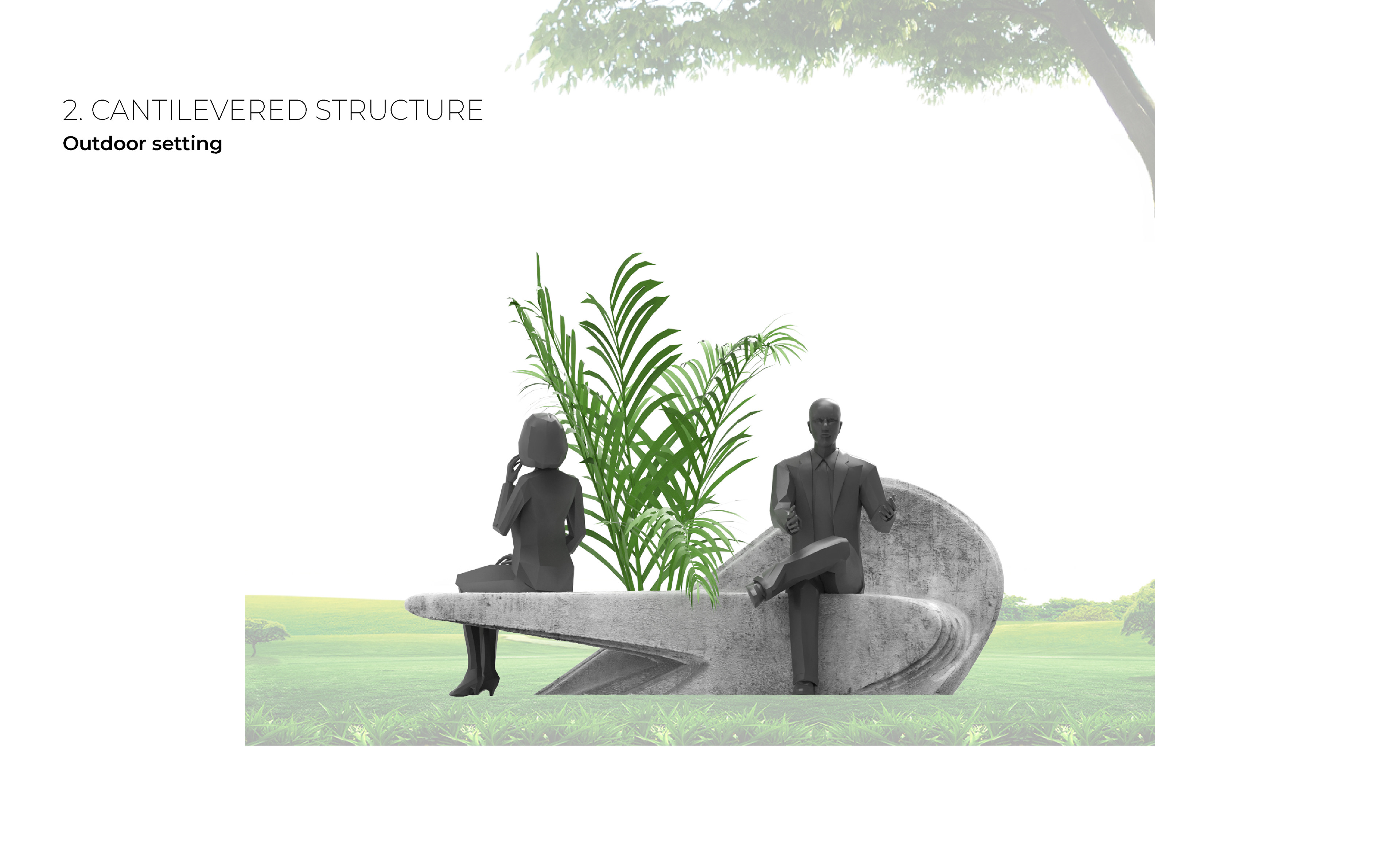
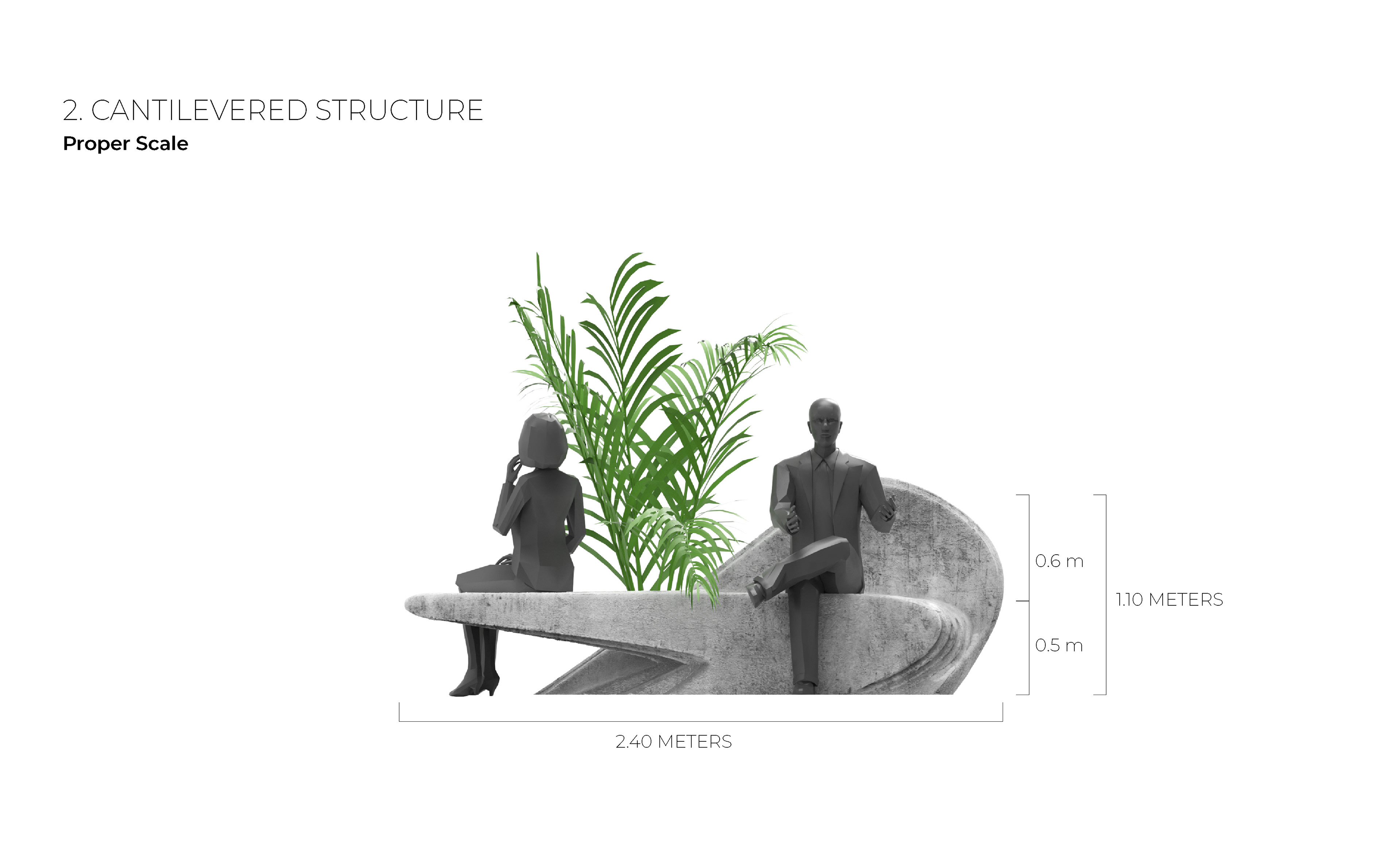
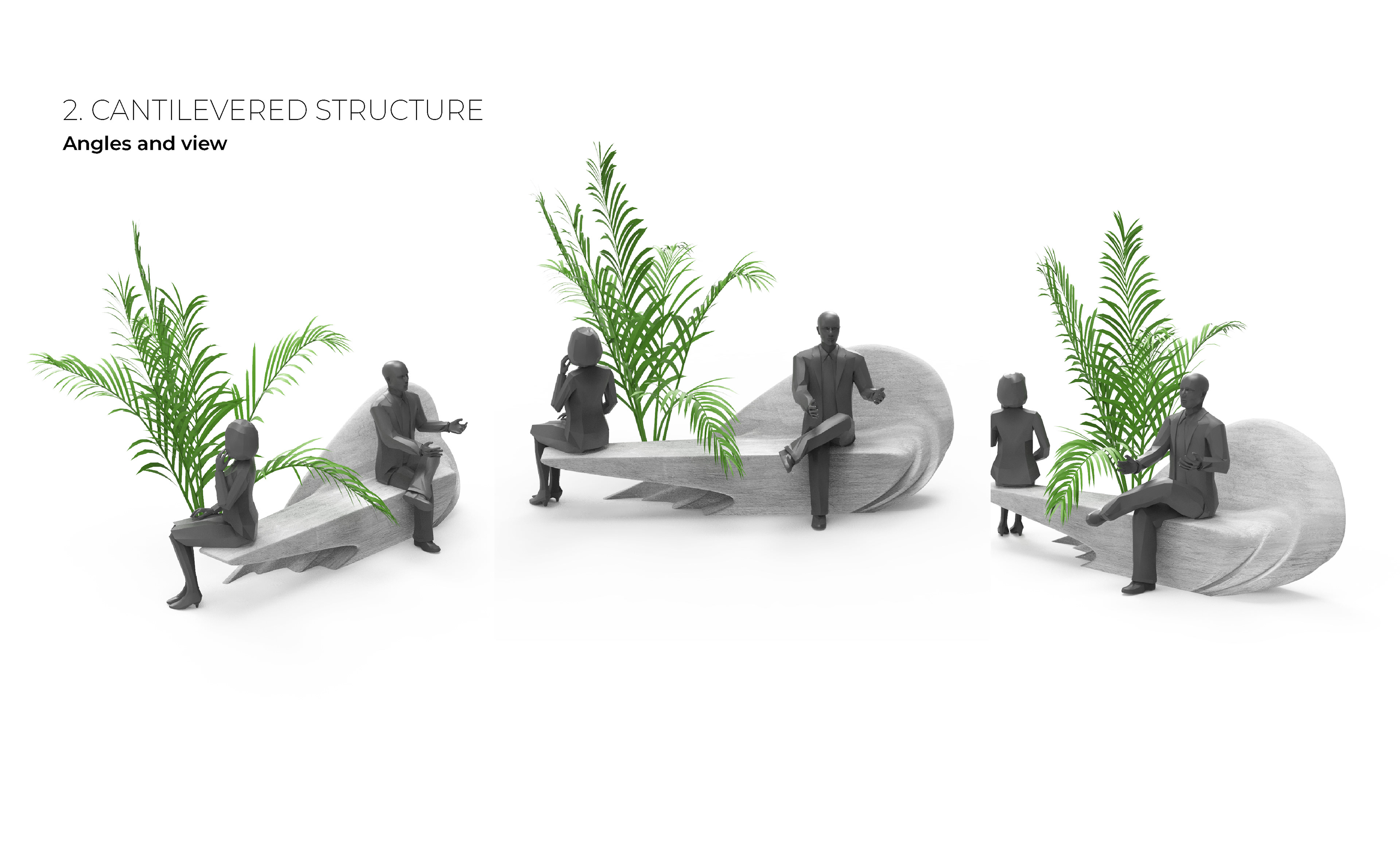
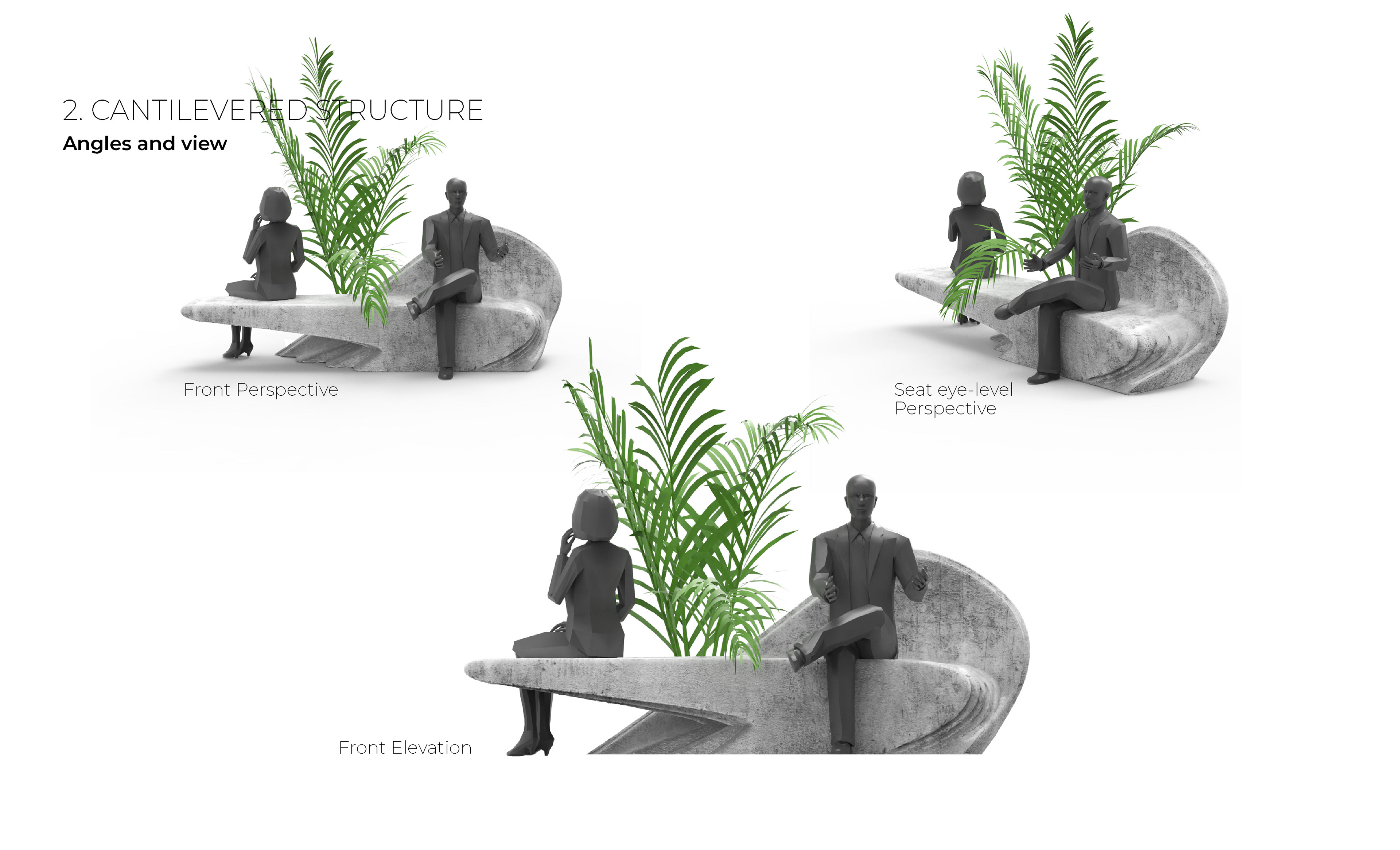
Then, we prepare and smooth out all the surfaces for proper finish and coated it with some plastering. This allow us to have one strong rigid body that can handle pressure and movement.
After that we build the concrete mold out of fiberglass because it could handle massive pressure and could be reused over and over.
Finally, the mold gets into position for casting, but before that, it take a 3D steel reinforcement inside to strengthen the concrete specially the cantilevered part and the back.
A final concrete cast looked exactly as it was meant to be. The concrete needed more testing and experimenting to optimally achieve the perfect looks, details and the nature of concrete without any additives or decorations. Decorations are added to make things looks better than they are, but we don’t need it here. Because it is already a masterpiece that speaks of itself.
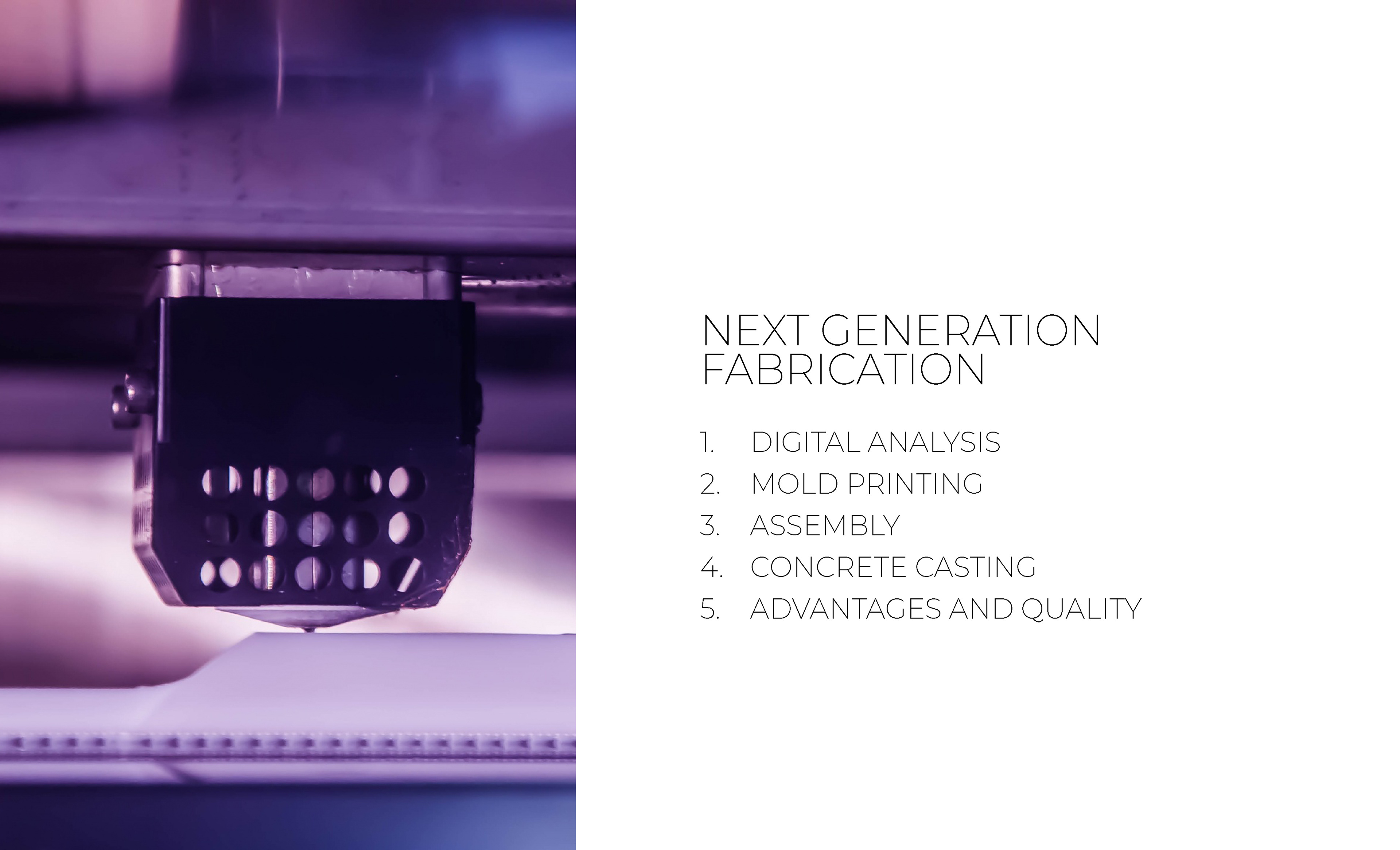
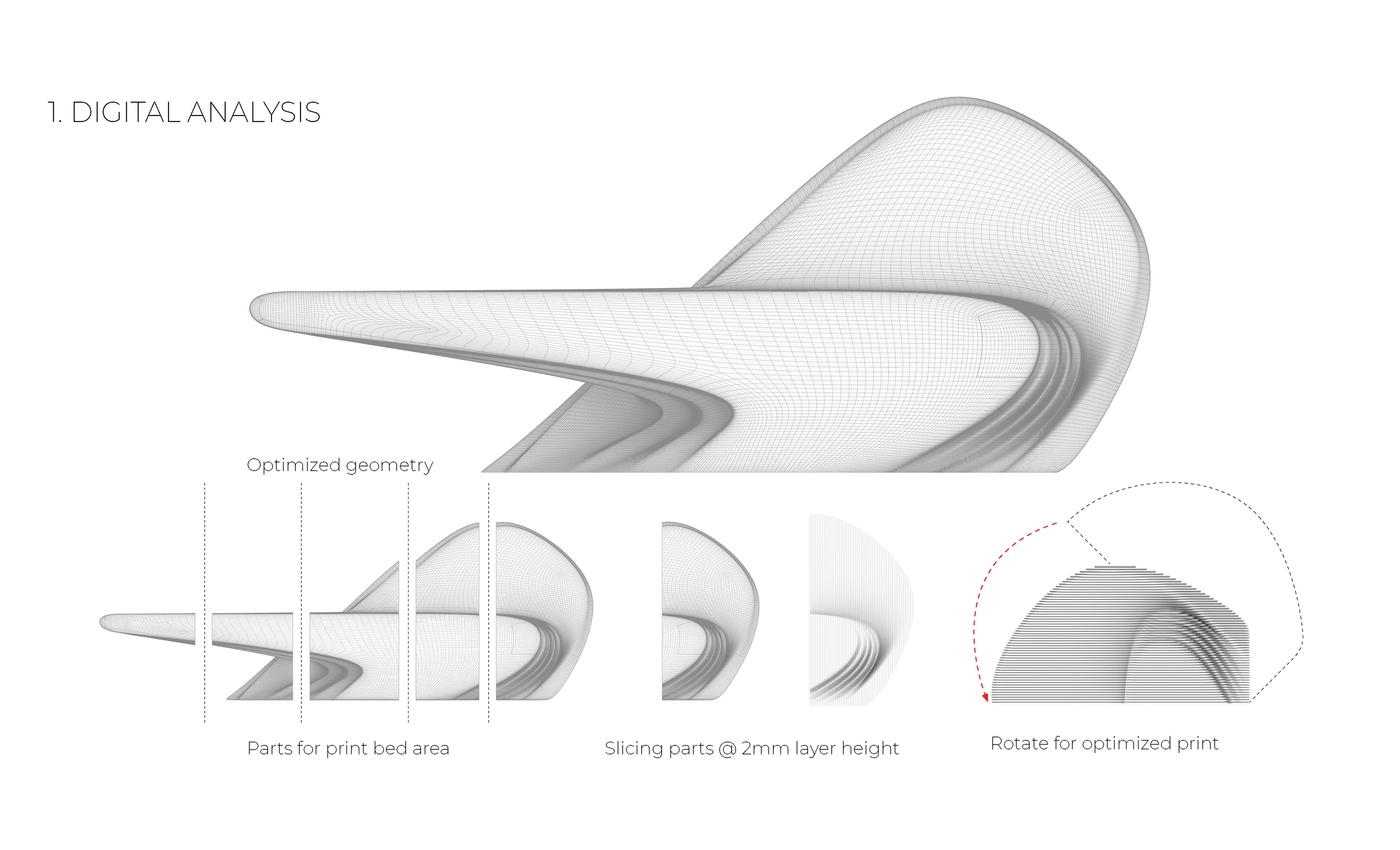
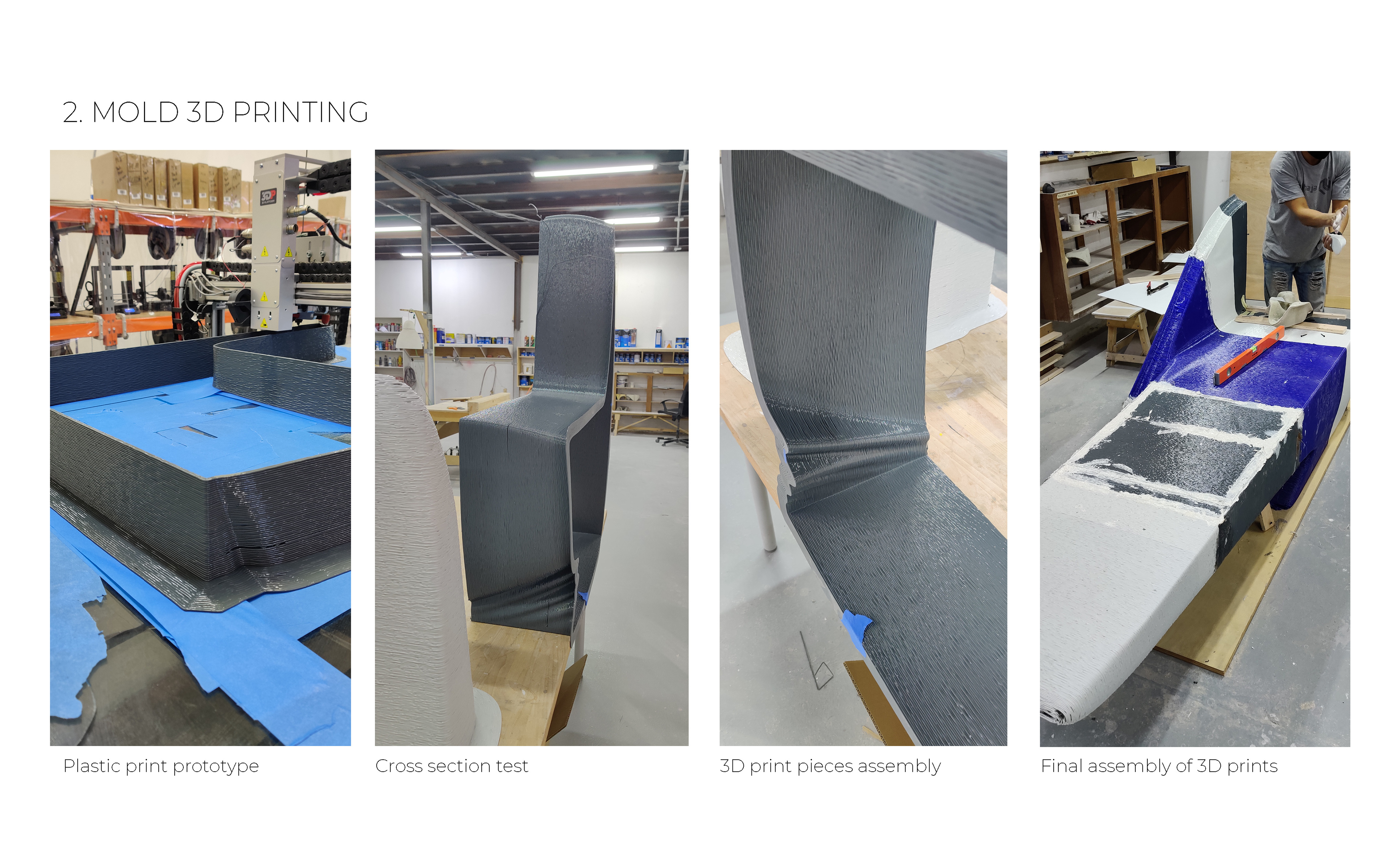
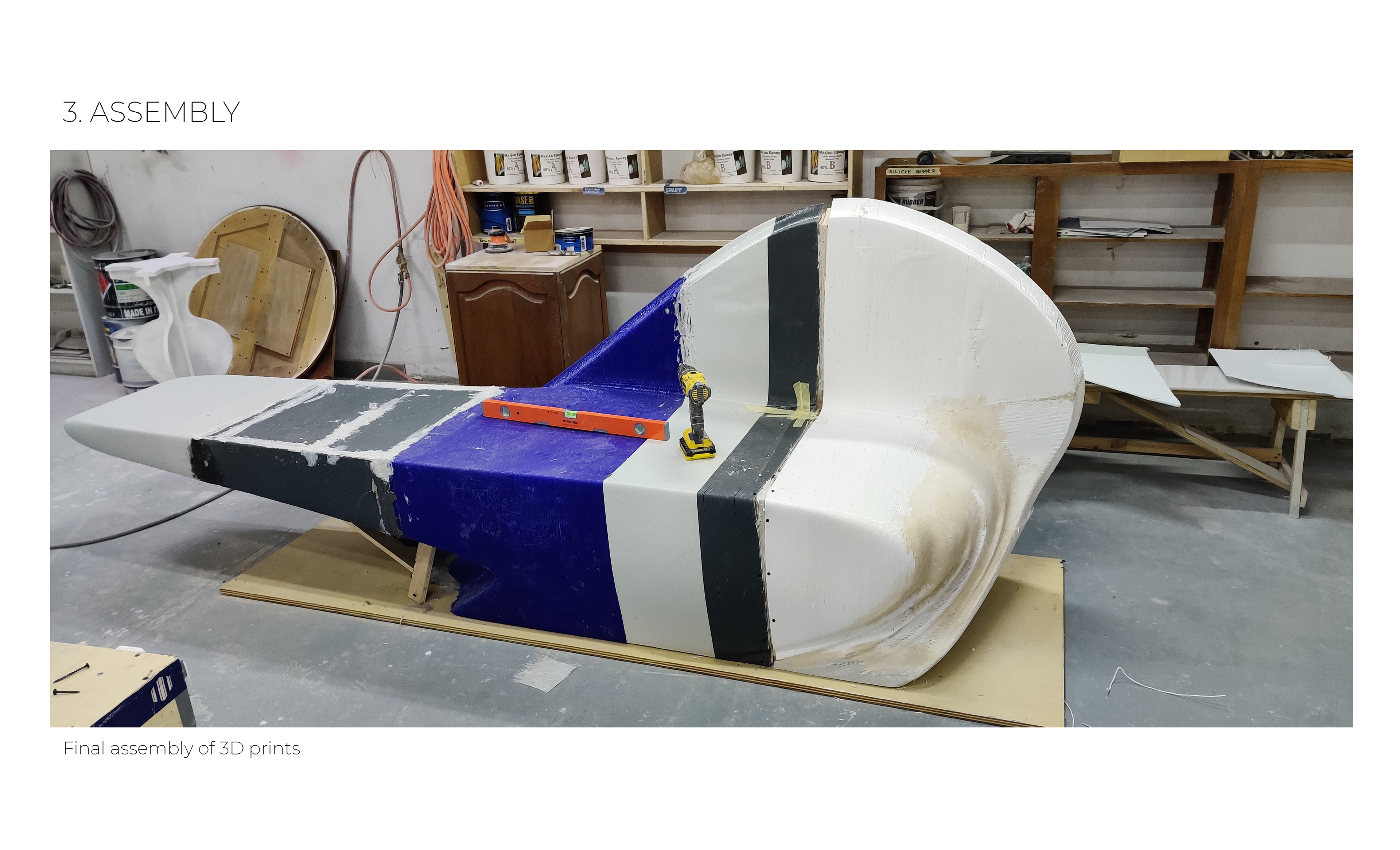
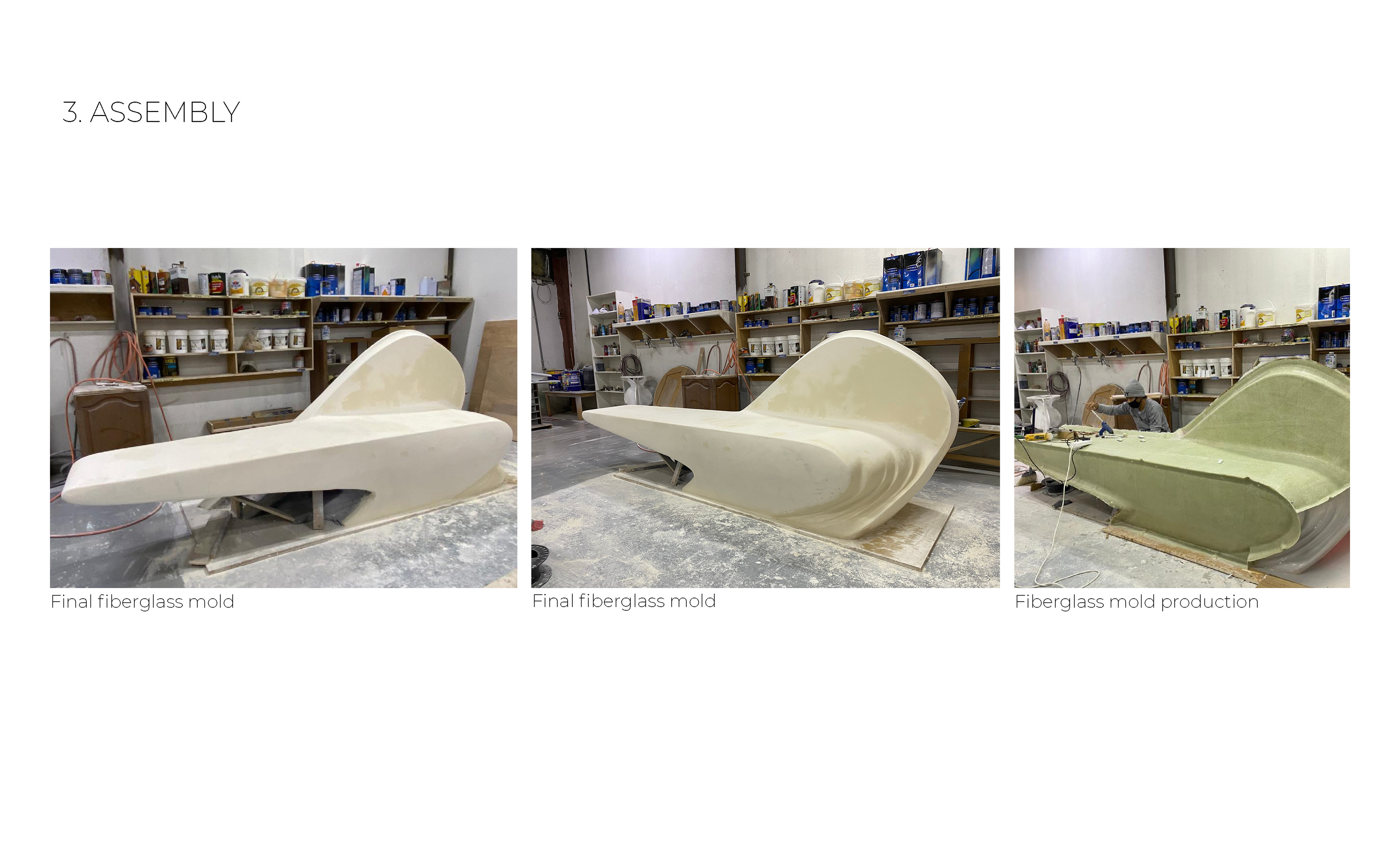
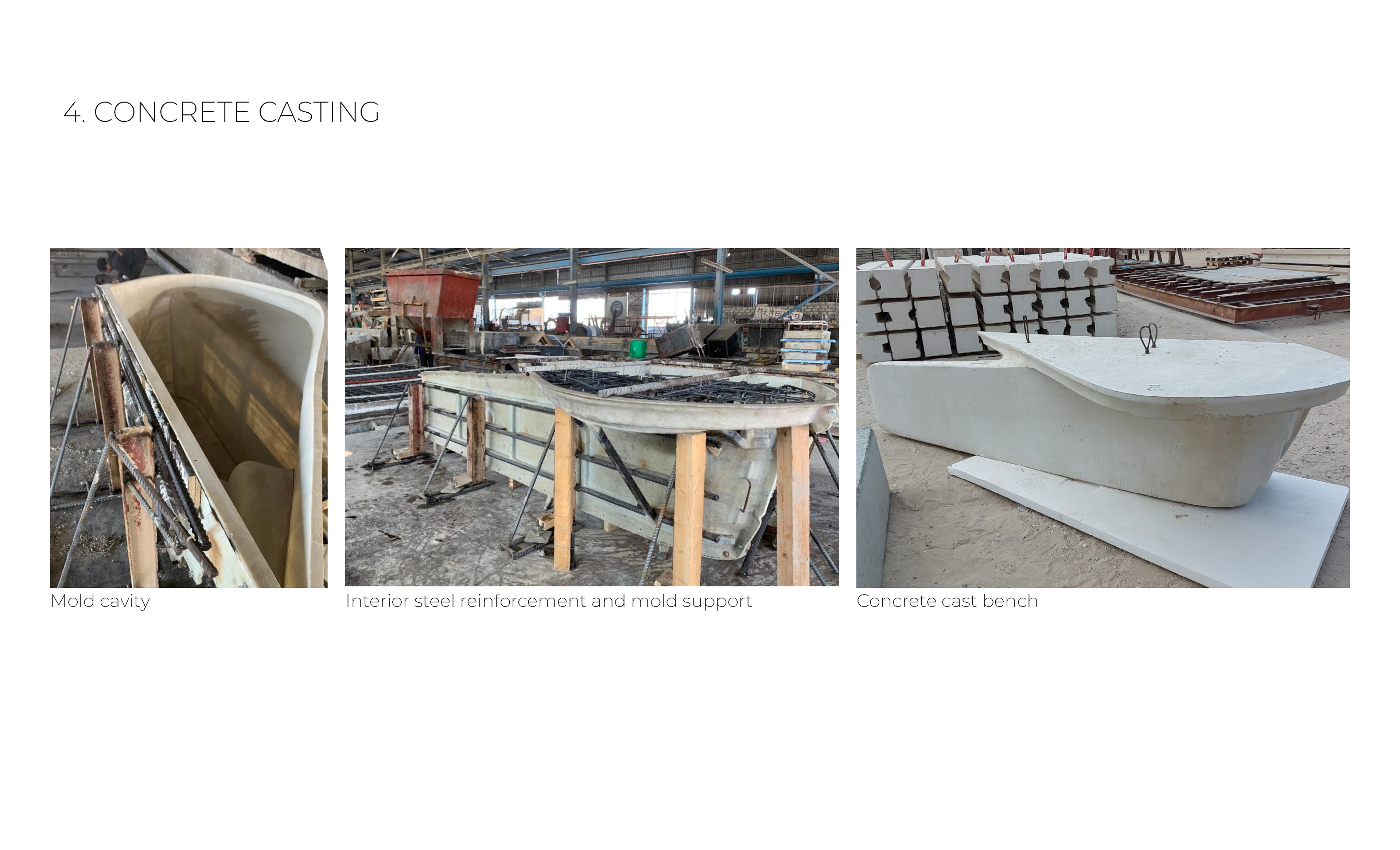
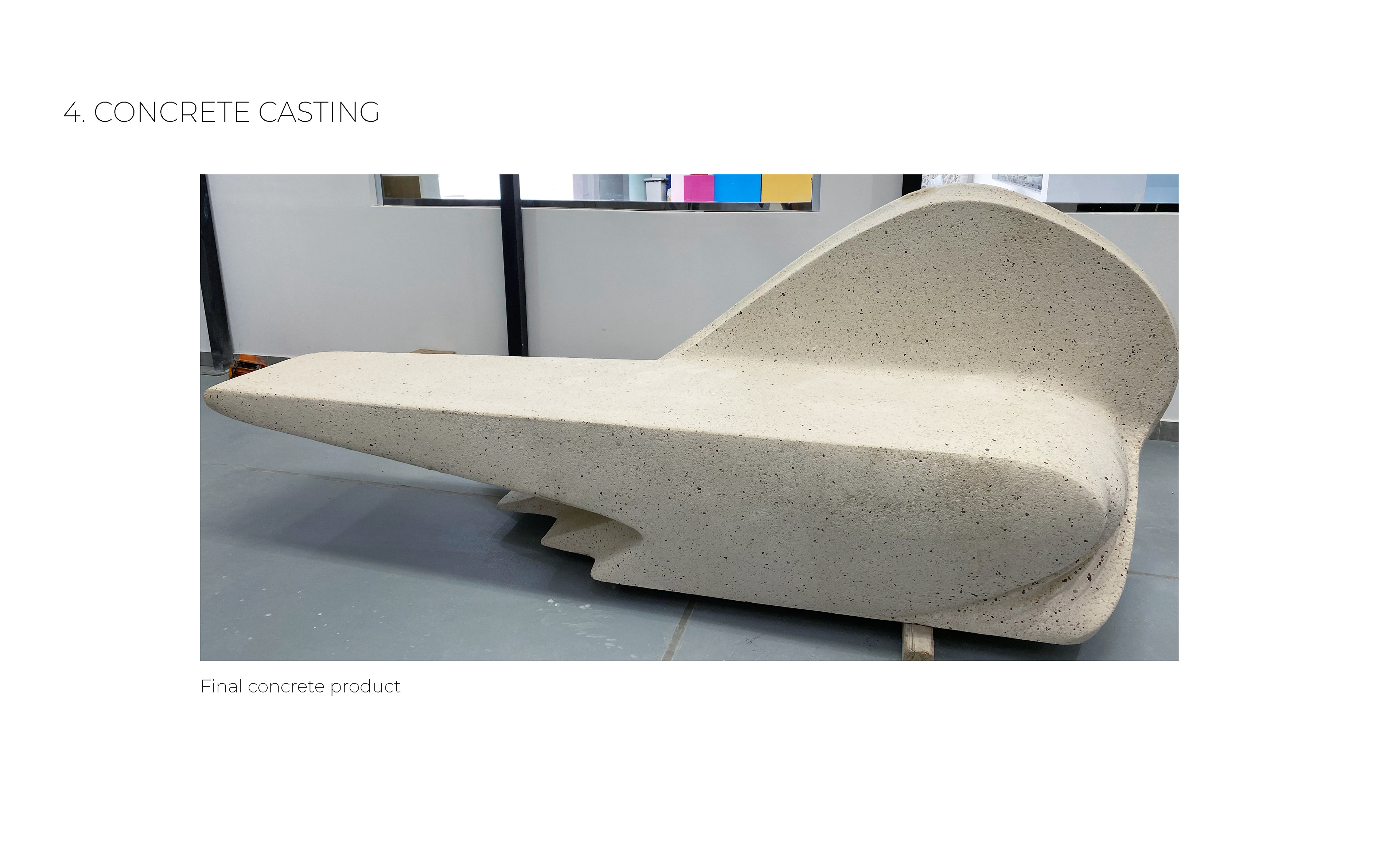
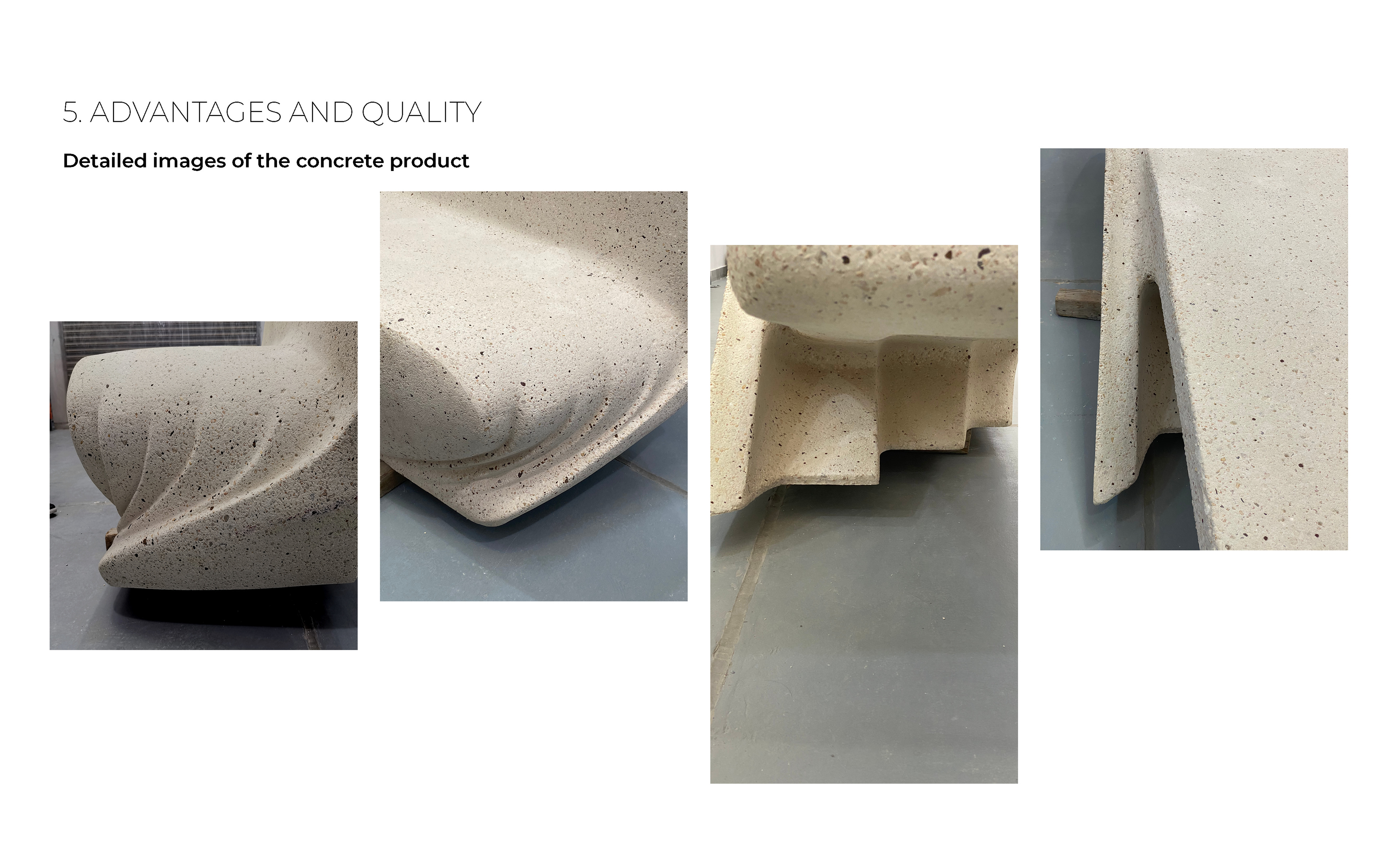
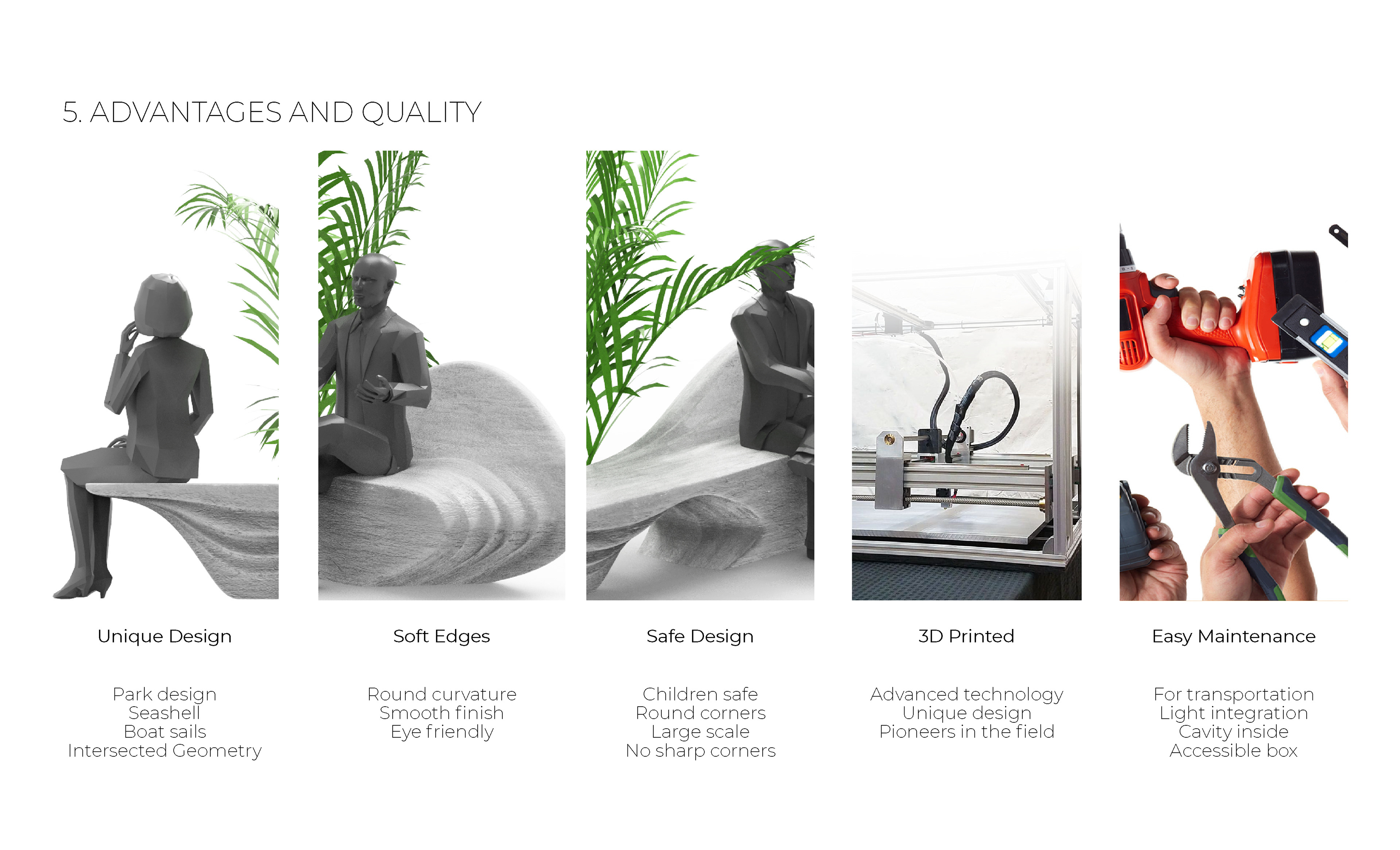
Finally, it is on the streets if you want to check them out.
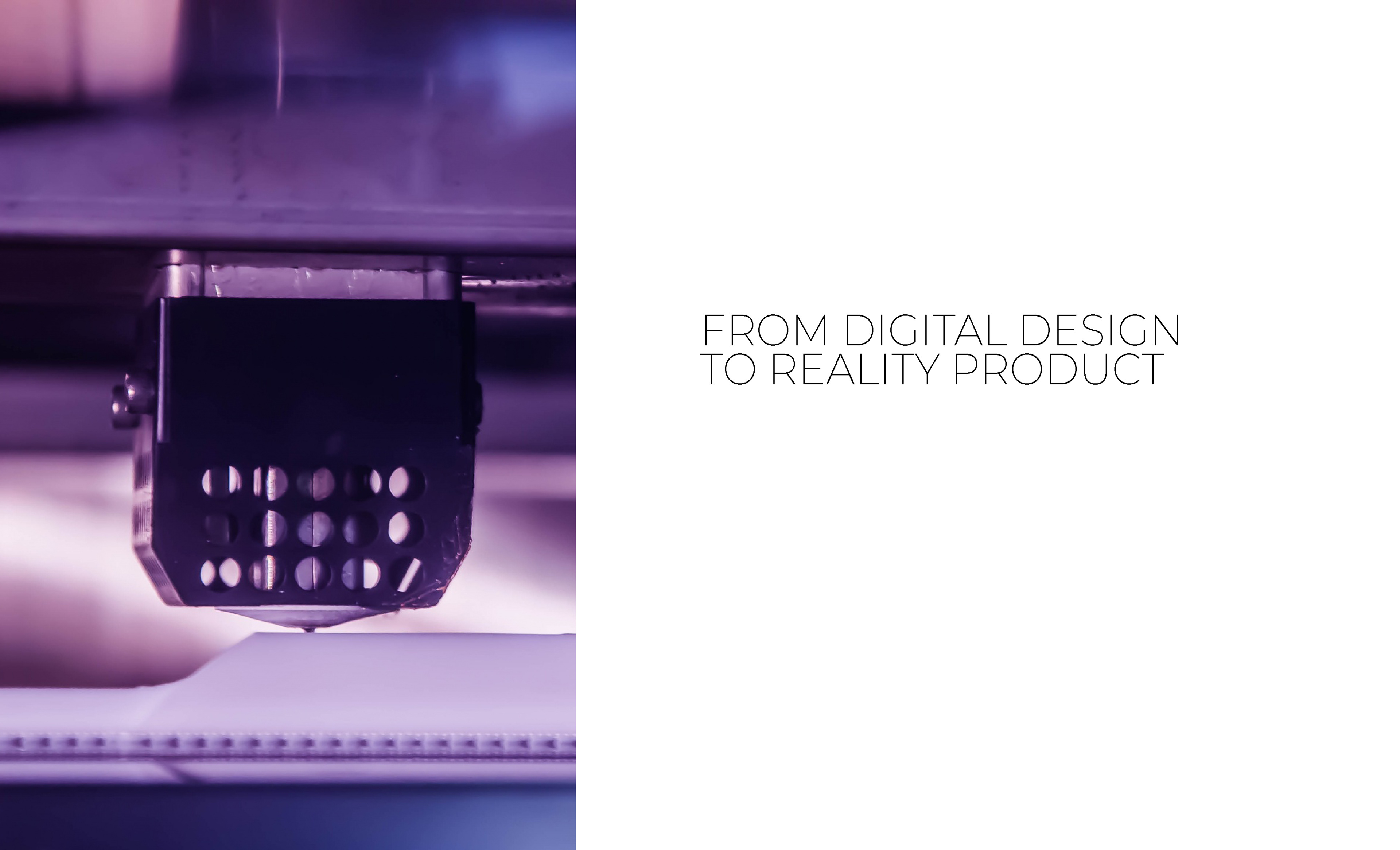
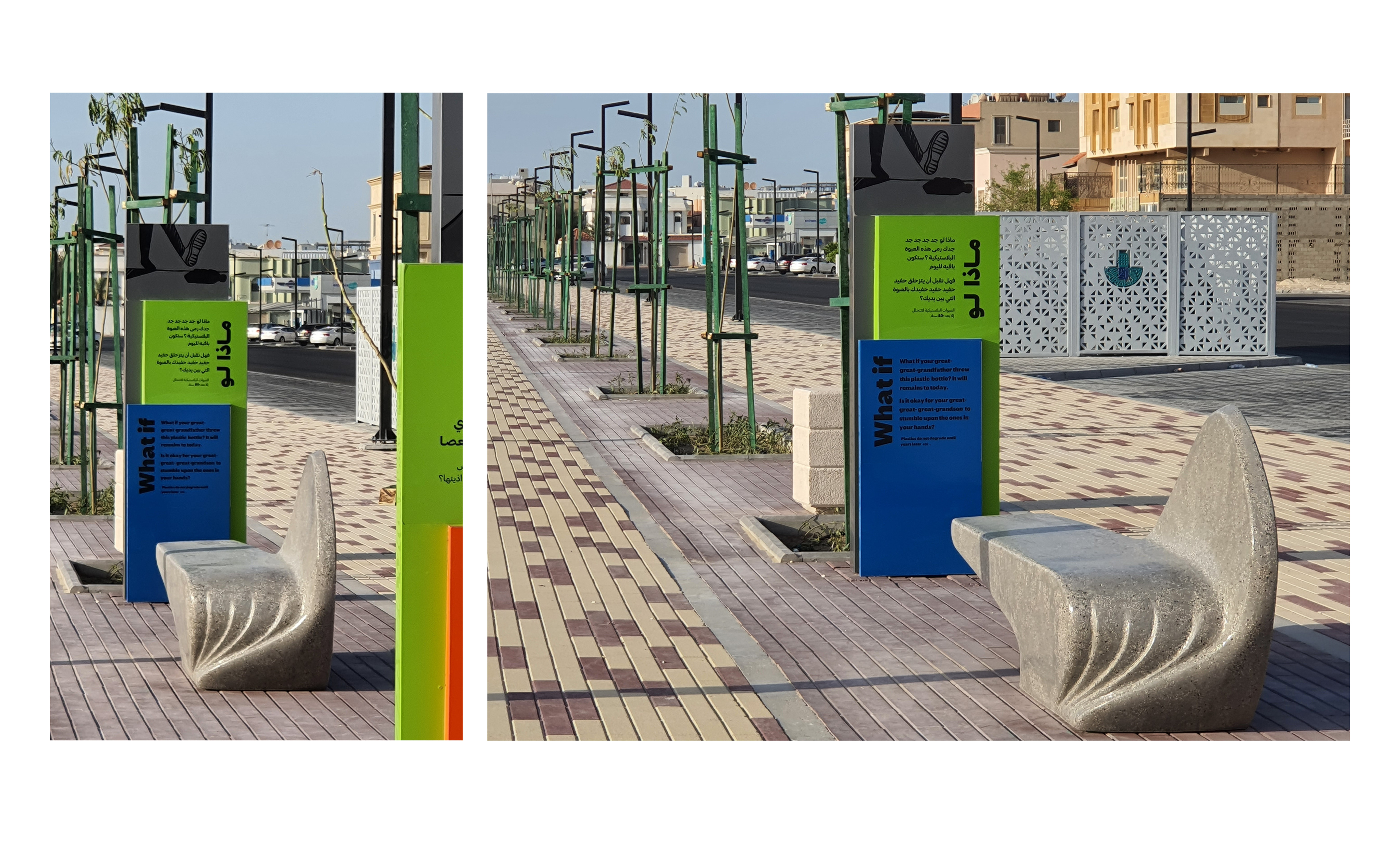
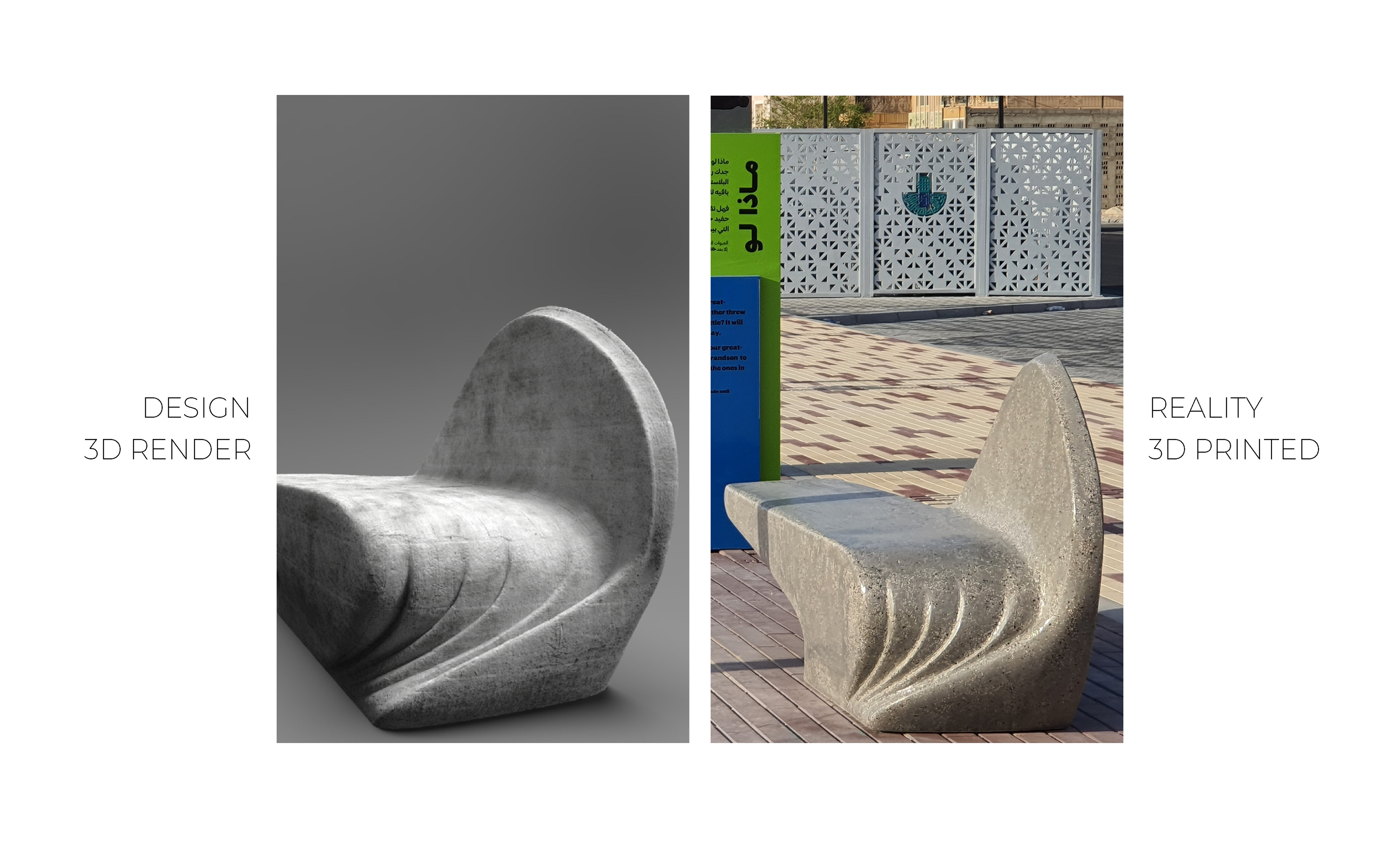
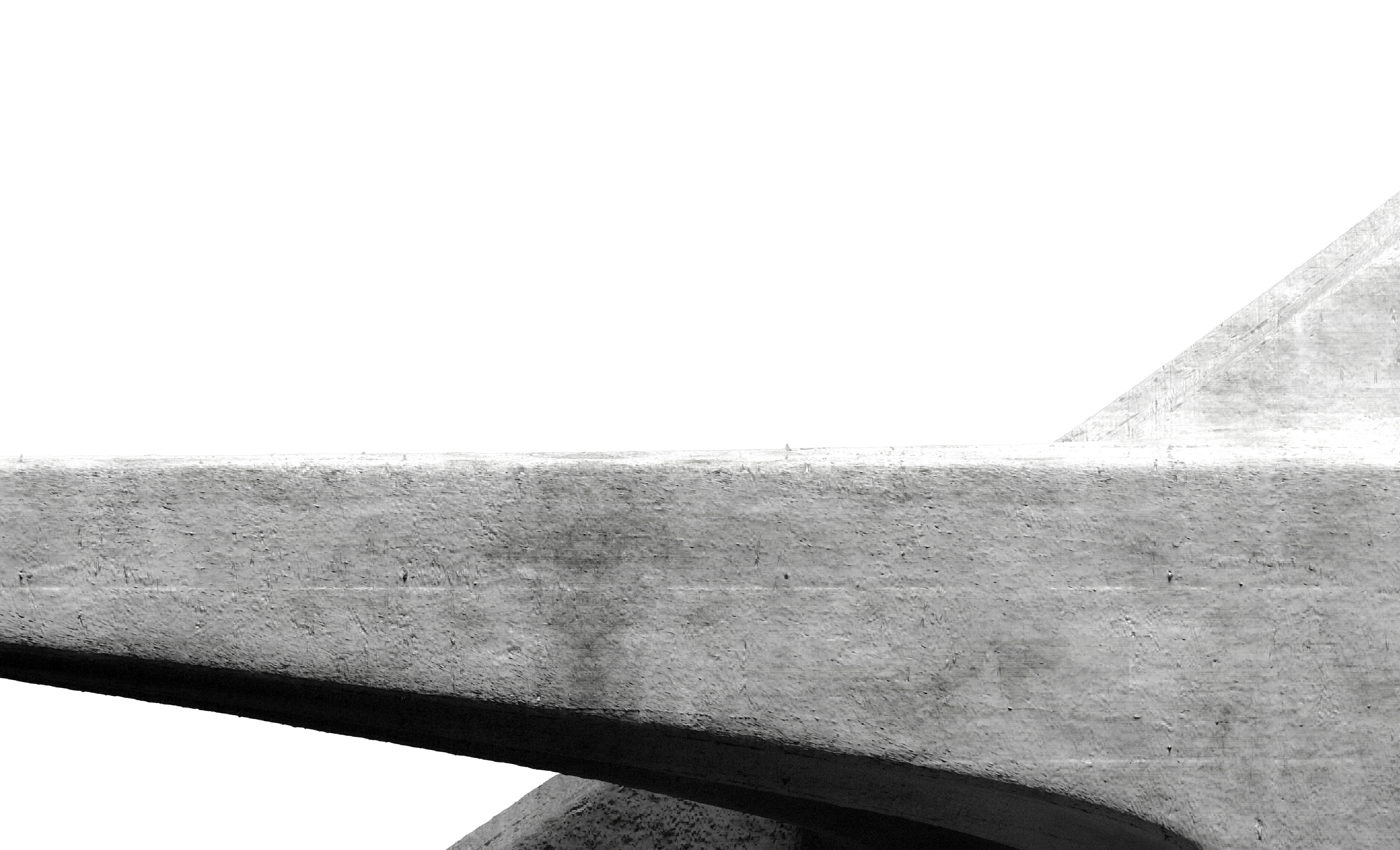